Introduction
Laser Cutting Machines
-
VIF-A Laser Cutting Machine
Rated 4.50 out of 5$12,500.00 – $34,000.00 Select options This product has multiple variants. The options may be chosen on the product page -
VIF Laser Cutting Machine
Rated 4.75 out of 5$17,300.00 – $70,000.00 Select options This product has multiple variants. The options may be chosen on the product page -
VIE Laser Cutting Machine
Rated 5.00 out of 5$21,800.00 – $166,500.00 Select options This product has multiple variants. The options may be chosen on the product page -
VIB Laser Cutting Machine
Rated 5.00 out of 5$21,300.00 – $166,000.00 Select options This product has multiple variants. The options may be chosen on the product page -
VIP Laser Cutting Machine
Rated 4.75 out of 5$25,800.00 – $170,500.00 Select options This product has multiple variants. The options may be chosen on the product page -
VIH Laser Cutting Machine
Rated 4.75 out of 5$92,000.00 – $420,000.00 Select options This product has multiple variants. The options may be chosen on the product page -
VIF-T Laser Cutting Machine
Rated 4.75 out of 5$34,300.00 – $179,000.00 Select options This product has multiple variants. The options may be chosen on the product page -
VIE-T Laser Cutting Machine
Rated 4.75 out of 5$43,300.00 – $188,000.00 Select options This product has multiple variants. The options may be chosen on the product page -
VIP-T Laser Cutting Machine
Rated 5.00 out of 5$68,800.00 – $213,500.00 Select options This product has multiple variants. The options may be chosen on the product page -
VIT Laser Cutting Machine
Rated 4.75 out of 5$24,300.00 – $167,500.00 Select options This product has multiple variants. The options may be chosen on the product page -
VIT-A Laser Cutting Machine
Rated 5.00 out of 5$79,300.00 – $222,500.00 Select options This product has multiple variants. The options may be chosen on the product page -
VIC Laser Cutting Machine
Rated 5.00 out of 5$3,000.00 – $7,500.00 Select options This product has multiple variants. The options may be chosen on the product page
Applications
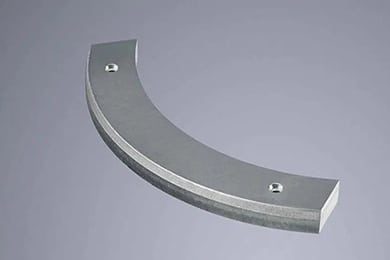
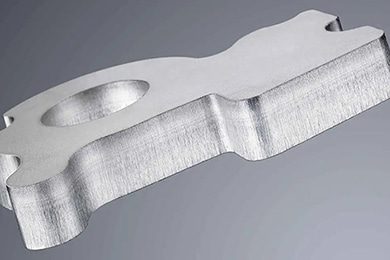
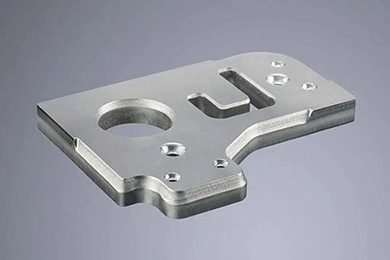
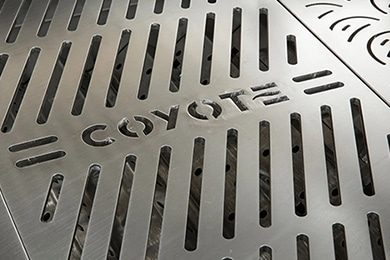
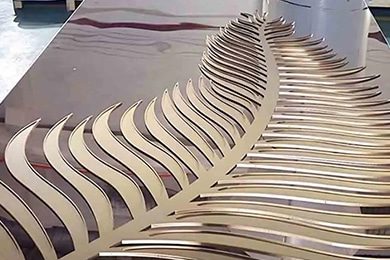
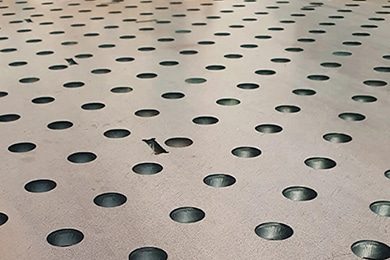
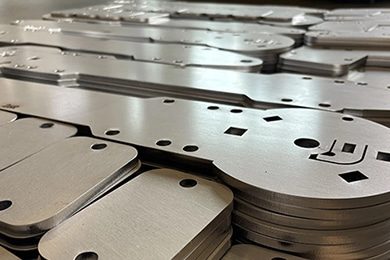
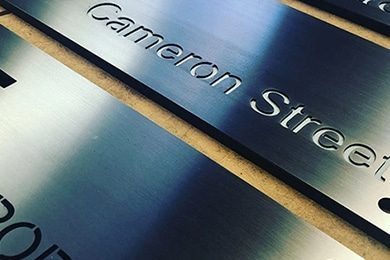
Advantages of Laser Cutting
Precision and Accuracy
Laser-cutting machines offer exceptional precision, capable of cutting intricate shapes and fine details with high accuracy. This ensures consistent results and minimal deviations, even for complex designs.
Minimal Material Waste
Laser cutting produces clean cuts with minimal kerf (cut width), reducing material wastage. The high precision of the process ensures that the maximum amount of material is used effectively, contributing to cost savings.
Versatility
Laser-cutting machines can handle a wide range of materials, including metals, plastics, wood, and ceramics. This versatility allows for applications across multiple industries, from automotive to signage, with the same machine.
High-Speed Processing
Laser cutting is a fast process, enabling high-speed operation without sacrificing quality. This increases production efficiency, making it ideal for both low and high-volume manufacturing.
Minimal Heat Affected Zone
The concentrated heat of the laser results in a very small heat-affected zone, reducing the risk of warping, distortion, or material damage. This ensures clean, sharp edges without compromising the integrity of the material.
Low Maintenance
Laser cutting machines require minimal maintenance compared to traditional cutting methods. With fewer moving parts, they are less prone to wear and tear, making them cost-effective in the long term.
Comparison with Other Cutting Methods
Feature | Laser Cutting | Water Jet Cutting | Plasma Cutting | Flame Cutting |
Precision | Very high precision, ideal for intricate cuts | High precision, especially for soft materials | Lower precision, suitable for thicker materials | Moderate precision, best for thick metals |
Material Versatility | Can cut metals, plastics, wood, ceramics, and more | Can cut metals, plastics, stone, glass, ceramics | Primarily metals, especially thicker materials | Primarily metals, especially ferrous metals |
Cutting Speed | Very fast, optimal for both small and large runs | Slower than laser cutting, ideal for thick materials | Faster than laser cutting, especially for thick materials | Slower than plasma and laser cutting, mostly for thick metals |
Heat Affected Zone (HAZ) | Very small HAZ, minimal distortion | Minimal HAZ, especially with low thermal conductivity materials | Larger HAZ, leading to material distortion | Larger HAZ, can cause warping and burn marks |
Edge Quality | Smooth, clean edges with minimal post-processing | Smooth edges, though may require finishing | Rougher edges, often needing cleanup | Rough edges with oxidation, requires significant finishing |
Material Thickness | Best for thin to medium materials, fiber lasers for thicker cuts | Great for cutting very thick materials | Ideal for thicker materials (up to 100mm) | Best for very thick metals, especially over 10mm |
Cost Efficiency | Efficient for both small and large batches, low material waste | High operating costs, ideal for thick materials | Cost-effective for thick materials, high energy use | Economical for cutting thick steel, but less efficient for thin materials |
Ease of Operation | User-friendly, automated settings | Requires skilled operators, abrasive handling | Easier to operate, but noisy and requires ventilation | Relatively simple, but requires careful monitoring of gas levels |
Environmental Impact | Low emissions, minimal material waste | Minimal fumes, but water disposal issues | High energy consumption, high noise, and fumes | Produces significant fumes, uses gases that require proper disposal |
Maintenance | Low maintenance, fewer moving parts | Requires regular maintenance, water and abrasive handling | Requires more maintenance, especially for electrodes and nozzles | Regular maintenance of cutting torch and gas supply needed |
Operating Cost | Lower operational cost, minimal waste | High operational cost due to water usage and abrasives | Moderate operational cost, high energy consumption | Lower operational cost, but consumables (gas) are significant |
Customer Reviews
Frequently Asked Questions
How Much Do Laser Cutting Machines Cost?
- Fiber Laser Cutting Machines: These machines typically range from $15,000 to $250,000, depending on the power (ranging from 1000W to 40kW), size, and advanced features such as automation, cooling systems, and software integration. Fiber lasers are ideal for cutting metals, providing high precision and efficiency.
- CO2 Laser Cutting Machines: The price range for CO2 laser cutting machines is generally between $3,500 and $15,000, depending on the machine’s specifications. CO2 lasers are commonly used for cutting non-metal materials like wood, acrylic, and plastics, and are popular for their versatility and lower initial cost.
What Is The Main Hazard With Laser Cutting Machines?
- Other Key Hazards Include:
- Skin Burns: Direct exposure to the laser beam or hot surfaces on the machine can cause severe burns to the skin.
- Exposure to Harmful Fumes and Gases: Laser cutting, especially of metals, produces fumes and gases (such as ozone, carbon monoxide, and particulate matter) that can be harmful to health if inhaled over time.
- Fire Hazard: The intense heat from the laser can ignite nearby combustible materials, leading to fire risks, particularly when cutting organic materials like wood, plastics, or fabrics.
- Electric Shock: Laser cutting machines often operate with high-voltage power supplies, creating a risk of electrical shock if proper safety procedures aren’t followed during operation or maintenance.
- Mechanical Injuries: Moving parts of the laser cutting machine, such as the gantry, robotic arms, or moving cutting heads, can cause physical injury if operators get too close during operation.
- Preventative Measures:
- Eye Protection: Operators should always wear laser-specific protective eyewear.
- Ventilation and Filtration: Use of proper exhaust systems and fume extractors to remove harmful gases and particles.
- Fire Safety: Ensure the cutting area is clear of flammable materials and have fire extinguishers nearby.
- Proper Training: Operators should be trained on safe practices and understand the hazards of the machine.
- Maintenance: Regular checks and proper machine maintenance are essential to minimize electrical or mechanical risks.
What Materials Cannot Be Cut on Laser Cutting Machines?
- Reflective Metals
- Reason: Laser cutting relies on the absorption of the laser energy by the material. Highly reflective metals like copper, brass, and aluminum reflect much of the laser beam, making it difficult to effectively cut through them. This can cause the laser to bounce back, potentially damaging the machine or causing a dangerous reflection of the beam.
- Alternative: Fiber laser cutting machines with high-power settings can cut some of these metals, but special precautions and settings are needed.
- Polyvinyl Chloride (PVC)
- Reason: PVC and other chlorinated plastics release toxic fumes, such as hydrogen chloride gas, when exposed to the laser. These fumes are not only harmful to human health but can also damage the laser-cutting machine’s internal components, such as the lenses.
- Alternative: Other plastics like acrylic or polycarbonate can be safely cut, but PVC should be avoided.
- Fiberglass
- Reason: Fiberglass is a composite material made of glass fibers embedded in a resin matrix. When laser cut, the glass fibers can melt, creating a rough edge, while the resin can emit toxic fumes. The combination of these issues makes it an unsuitable material for laser cutting.
- Alternative: Water jet cutting or mechanical cutting are better options for fiberglass.
- Lead and Other Toxic Materials
- Reason: Materials such as lead and other heavy metals can emit hazardous fumes when cut by a laser, which poses serious health risks. Lead fumes, in particular, are extremely toxic.
- Alternative: Avoid cutting lead, and use more suitable materials like stainless steel or aluminum when necessary.
- Polycarbonate
- Reason: While polycarbonate is technically cuttable with a laser, it tends to yellow or burn at the cut edges due to its composition, which can result in undesirable aesthetics. Additionally, it can produce harmful fumes during the cutting process.
- Alternative: Acrylic is often preferred over polycarbonate because it cuts cleanly and without the burning issue.
- Stone and Ceramics
- Reason: Stone and ceramics are hard, dense materials that cannot absorb enough laser energy to effectively melt and vaporize the material. This makes cutting them with a laser impractical.
- Alternative: Water jet cutting or diamond-tipped saws are better choices for stone and ceramics.
- Rubber
- Reason: When rubber is cut by a laser, it can burn and produce thick, harmful fumes. The fumes produced by burning rubber are often unpleasant and can be harmful to both the operator and the machine.
- Alternative: Mechanical methods like die cutting or water jet cutting are often used for rubber materials.
- Certain High-Carbon Steels
- Reason: High-carbon steels, especially those with a high amount of alloying elements, can be difficult to cut because they may cause the laser to deflect or scatter. Additionally, they tend to form a tough oxide layer that can affect the quality of the cut.
- Alternative: Plasma cutting or water jet cutting can be more effective for these materials.
- Glass
- Reason: While glass can technically be cut with a laser, it is not commonly done due to the material’s brittleness and the challenges in controlling the heat, which can lead to cracking. Glass also does not absorb laser energy well.
- Alternative: Diamond cutters or water jet cutters are more suitable for cutting glass.
- Materials Containing Hydrogen or Halogens
- Reason: Teflon and similar materials, such as some fluoropolymers, contain hydrogen and halogens, which can release toxic gases when exposed to the laser. These gases are harmful to health and can corrode the cutting machine’s components.
- Alternative: If you need to cut Teflon or similar materials, consider alternative methods like water jet cutting.
How Do I Choose Laser-Cutting Machines?
- Material Type and Thickness
- Material Compatibility: Determine the types of materials you will primarily cut, such as metals, plastics, wood, or composites. Different lasers are optimized for different material types.
- Thickness: Check the machine’s capacity to cut through the thickness of the materials you will use. Ensure the machine can handle the maximum thickness your projects require.
- Laser Type
- CO2 Lasers: Ideal for cutting non-metals like wood, acrylic, and plastic. CO2 lasers are generally more affordable but are not as effective for cutting metals.
- Fiber Lasers: Best for cutting metals like steel, aluminum, and brass. Fiber lasers offer faster cutting speeds, higher precision, and better energy efficiency, especially for metalworking.
- Power Requirements
- Laser Power: Higher-power lasers enable faster cutting of thicker materials. Laser power typically ranges from 30W to over 40kW. The higher the power, the thicker the material you can cut.
- Electrical Requirements: Ensure that your facility can support the machine’s power needs, including sufficient electrical capacity and a stable power supply.
- Cutting Area and Size
- Work Area Dimensions: The cutting bed size should accommodate the largest material pieces you plan to cut. Ensure the machine can handle the dimensions of your typical workpieces.
- Footprint: Consider the physical space available in your workshop or factory. Some laser-cutting machines require a substantial amount of floor space.
- Precision and Accuracy
- Tolerance: Evaluate the level of precision required for your applications. If you’re cutting intricate designs, high precision is essential.
- Repeatability: A reliable machine should provide consistent accuracy and repeatability across multiple cuts.
- Speed and Efficiency
- Cutting Speed: A faster cutting machine increases productivity and reduces turnaround time. Ensure the machine’s cutting speed meets your production goals.
- Automation: Features like automatic loading/unloading, automatic focusing, or automated nesting software can significantly improve efficiency and reduce labor costs.
- Software and Controls
- Ease of Use: The software should be user-friendly, allowing for quick setup and operation. This reduces the learning curve for your operators.
- Compatibility: Ensure that the machine’s software can handle the design files you typically work with (e.g., DXF, DWG, SVG).
- Maintenance and Support
- Reliability: Choose a machine from a well-established manufacturer with a reputation for durability and reliability.
- Support and Warranty: Look for a machine with solid after-sales support, including customer service, technical support, and a comprehensive warranty.
- Cost and Budget
- Initial Cost: Laser-cutting machines can range from affordable models to high-end machines. Make sure you find one that fits your budget but also provides the necessary capabilities for your applications.
- Operating Costs: Consider ongoing expenses such as power consumption, maintenance, and the cost of replacement parts (e.g., lenses and nozzles).
- Safety Features
- Safety Guards and Enclosures: The laser-cutting machine should be equipped with adequate protection against laser exposure and flying debris.
- Fume Extraction: Laser cutting generates fumes, especially when cutting plastics or metals. Ensure the machine has a robust fume extraction system to maintain a safe working environment.
- Application-Specific Requirements
- Special Features: Depending on your industry, you may need specific features like rotary attachments for tube cutting, advanced cooling systems, or specialized cutting heads for specific materials.
- Customization Options: If you require tailored capabilities, check if the machine offers options for customization to meet your specific needs.
How Precise Are Laser Cutting Machines?
- Accuracy and Tolerance
- Laser-cutting machines typically have an accuracy (or tolerance) in the range of ±0.1 mm to ±0.005 mm, depending on the machine’s quality and the material being cut.
- High-end fiber lasers tend to offer greater accuracy, with tolerances as tight as ±0.02 mm in some cases.
- Beam Focus and Spot Size
- Laser cutting precision is heavily influenced by the beam focus. A smaller spot size allows for finer, more detailed cuts, making the machine highly precise.
- The beam diameter can be as small as 0.1 mm for fiber lasers, which contributes to their ability to cut very fine lines and intricate patterns.
- Kerf Width
- The kerf is the width of the material removed by the laser beam during cutting. It typically ranges from 0.1 mm to 0.5 mm depending on the laser type, material, and power settings.
- Fiber lasers tend to produce narrower kerf widths compared to CO2 lasers, contributing to higher precision in cutting and less material waste.
- Repeatability
- Repeatability refers to the ability of a laser-cutting machine to produce identical cuts over multiple cycles. High-quality laser cutting machines, especially those with CNC controls, can achieve consistent repeatability within ±0.05 mm or better.
- This is critical in applications where multiple identical parts are being produced.
What Is The Expected Lifespan of Laser Cutting Machines?
- Type of Laser
- Fiber Lasers: Fiber laser cutting machines generally have a longer lifespan compared to CO2 lasers, due to their solid-state design and fewer moving parts. With proper maintenance, fiber lasers can easily last 20 years or more.
- CO2 Lasers: CO2 lasers, while effective, tend to have a shorter lifespan due to the wear and tear on the laser tube. The laser tube typically lasts between 8,000 to 12,000 hours of use before it requires replacement. The overall lifespan of the machine can still reach 10-15 years with proper upkeep.
- Usage Patterns
- Machines used for high-volume production or in demanding environments may wear out faster due to the constant operation and stress on components.
- Low-volume or intermittent use may extend the lifespan of the machine, especially if it’s properly maintained.
- Maintenance and Care
- Regular maintenance is crucial to extending the lifespan of laser-cutting machines. Routine tasks such as cleaning the optics, replacing filters, and checking the cooling systems can prevent major issues and help the machine run efficiently.
- Preventive maintenance programs from the manufacturer or third-party service providers can increase the machine’s longevity and performance.
- Quality of the Machine
- High-quality machines from reputable manufacturers are built with durable components and may last longer with minimal issues.
- Budget or lower-quality models may not have the same durability and could experience more frequent breakdowns or performance degradation over time.
- Laser Source and Power Supply
- The laser source itself (whether it’s a fiber laser or CO2 laser tube) will eventually degrade with use, particularly the CO2 laser tubes, which have a limited lifespan of 8,000 to 12,000 operating hours.
- The power supply can also impact the machine’s overall lifespan. Overvoltage, power surges, and improper handling can damage sensitive components, reducing the machine’s longevity.
- Environmental Factors
- Environmental conditions such as dust, temperature fluctuations, and humidity can affect the longevity of the machine. Machines operating in a clean, controlled environment tend to last longer and experience fewer issues.
- Machines used in harsh or industrial environments with significant dirt, humidity, or high temperatures may face accelerated wear and tear.
How Much Power Do Laser Cutting Machines Consume?
- CO2 Laser Cutting Machines
- Laser Power: CO2 lasers typically range from 40W to several kilowatts (kW).
- Power Consumption: A small CO2 laser cutting machine (e.g., 40W to 600W) may consume around 0.5 to 5 kW of electrical power, including the laser source, cooling system, and other components.
- Fiber Laser Cutting Machines
- Laser Power: Fiber lasers generally range from 1000W to over 20 kW.
- Power Consumption: The fiber laser cutting machine with a power output of 1 kW typically consumes around 7 to 9 kW of electrical power. High-power fiber lasers (e.g., 4 kW to 20 kW) can consume 25 to 90 kW or more, depending on the power level and efficiency.
- Additional Factors Affecting Power Consumption
- Cooling Systems: Laser cutting machines require cooling systems (air-cooled or water-cooled) to maintain optimal operating temperatures. These systems can add significant power consumption, ranging from a few hundred watts to several kilowatts, depending on the cooling method and machine size.
- Auxiliary Equipment: Additional equipment such as exhaust systems, air compressors, and control systems also contribute to the overall power consumption. This auxiliary equipment can add another 1 to 10 kW to the total power usage.
- Operational Settings: The power consumption varies with the operational settings, including cutting speed, material type, and thickness. Higher cutting speeds and thicker materials generally require more power.
What Customer Support Do Laser Cutting Machines Provide?
- Free Online Technical Support: Customers can access complimentary technical assistance through online platforms, including email, chat, or video support. This service is ideal for troubleshooting, software setup, or resolving operational issues remotely.
- Paid On-Site Training: For users requiring hands-on guidance, on-site training sessions are available at an additional cost. These sessions cover installation, operation, and maintenance to ensure optimal use of the machine.
Related Resources
Laser Marking VS Screen Printing
Laser Welding VS MIG Welding
Laser Rust Removal VS Sandblasting Rust Removal
Fiber Laser Cutting VS Plasma Cutting
Contact Us
Contact Information Form: