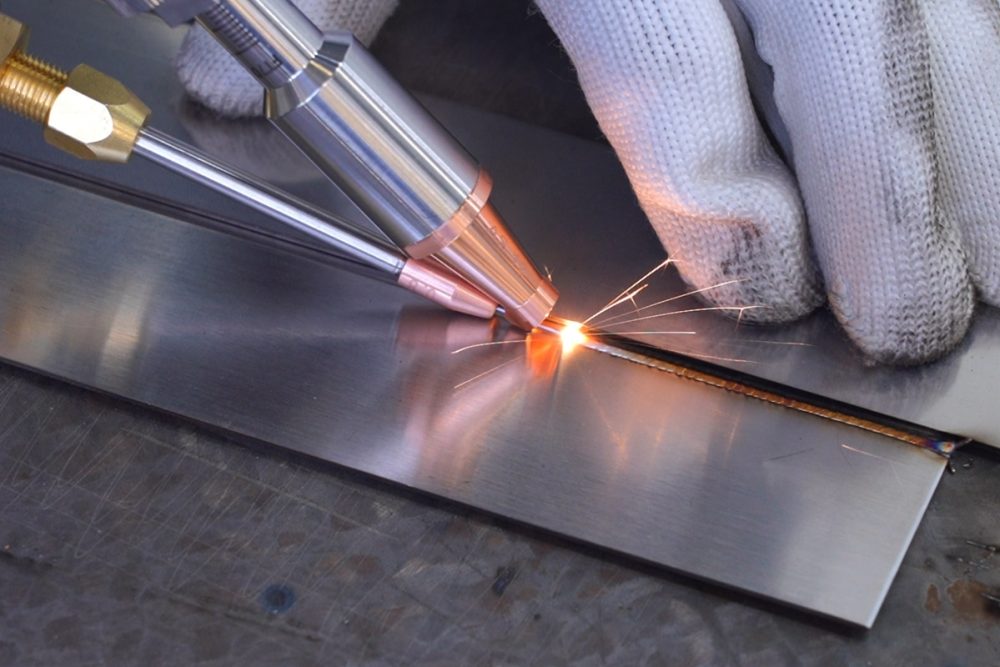
Overview of Welding Processes
What is Welding?
Historical Context of Welding
Understanding Laser Welding
Principles of Laser Welding
Laser welding works by concentrating high-energy laser beams onto the surface of metals, generating heat to melt and fuse them. The process can operate in two primary modes:
- Conduction Welding: The laser heats the surface of the metals, creating shallow welds ideal for thin materials.
- Keyhole Welding: A high-energy laser creates a deep and narrow cavity in the material, vaporizing it to produce deeper welds. This method is used for thicker metals and high-strength joints.
Types of Lasers Used in Welding
Different laser types are used depending on the specific application and material requirements:
- Fiber Lasers: Known for high efficiency and excellent beam quality, they are commonly used for precision welding in the automotive and aerospace industries.
- CO2 Lasers: Ideal for thick materials and large-scale applications due to their high power output.
- Nd: YAG Lasers (Neodymium-doped Yttrium Aluminum Garnet): Versatile for pulsed and continuous wave applications, often used in medical and micro-welding tasks.
- Diode Lasers: Compact and energy-efficient, these are suitable for specialized welding tasks and integration into robotic systems.
Key Parameters in Laser Welding
Successful laser welding depends on the precise control of several key parameters:
- Laser Power: Dictates the depth of penetration and weld speed.
- Welding Speed: Affects heat input, weld bead shape, and overall quality.
- Beam Focus Position: Determines the concentration of energy at the joint, critical for achieving clean welds.
- Shielding Gas: Commonly argon, helium, or nitrogen, shielding gas prevents oxidation and ensures a clean weld pool.
- Material Properties: Reflectivity and thermal conductivity of the metal influence the energy absorption and welding efficiency.
Advantages of Laser Welding
Laser welding offers numerous advantages over traditional methods:
- High Precision: Ideal for applications requiring intricate and accurate welds.
- Minimal Heat Distortion: The focused energy minimizes the heat-affected zone, preserving the base material’s properties.
- Speed and Efficiency: High welding speeds improve productivity, making it suitable for large-scale production.
- Versatility: Works on a variety of metals, including steel, aluminum, titanium, and alloys.
- Automation Compatibility: Easily integrates with robotic systems for mass production and consistency.
- Non-Contact Process: Reduces wear on tools and equipment, lowering maintenance costs.
Limitations and Challenges of Laser Welding
Despite its many advantages, laser welding has some limitations:
- High Initial Investment: Laser welding systems and setups are expensive, and require significant capital.
- Reflective Metals: Materials like copper and certain aluminum alloys can reflect the laser beam, reducing efficiency.
- Precision Requirements: Tight tolerances and exact joint preparation are critical for successful welding.
- Shielding Gas Use: Improper gas flow can lead to weld defects such as porosity or oxidation.
- Material Thickness: While effective for thin to medium-thickness metals, very thick materials may require additional processes or multiple passes.
Applications of Laser Welding
Laser welding is a versatile process used in a wide range of industries:
- Automotive Industry: For welding car body panels, gear assemblies, and battery modules.
- Aerospace and Defense: Precision joining of lightweight metals and critical components.
- Medical Devices: Ideal for producing implants, surgical tools, and other high-precision equipment.
- Electronics Industry: For micro-welding applications in semiconductors, sensors, and circuit boards.
- Jewelry and Luxury Goods: Creating seamless welds in intricate designs and precious metals.
- Energy Sector: Used in manufacturing solar panels, fuel cells, and pipelines.
Understanding MIG Welding
Principles of MIG Welding
The Role of Shielding Gas in MIG Welding
Shielding gas is essential in MIG welding to protect the weld pool from contamination by atmospheric gases like oxygen, nitrogen, and hydrogen. Without shielding, the weld could become porous, weak, or brittle. Commonly used shielding gases include:
- Argon: Provides a stable arc and is ideal for welding non-ferrous metals like aluminum.
- Carbon Dioxide (CO2): A cost-effective option, commonly used for steel welding, though it can produce more spatter.
- Argon-CO2 Mixtures: A balanced option, combining the benefits of both gases for better weld quality and reduced spatter.
- Helium: Often added to argon for deeper penetration and faster welding speeds, particularly for thicker materials.
Advantages of MIG Welding
MIG welding offers numerous benefits that make it a widely used welding process:
- Ease of Use: MIG welding is beginner-friendly due to its straightforward setup and operation.
- High Welding Speed: The continuous wire feed allows for faster weld deposition, improving productivity.
- Versatility: Suitable for a wide range of metals, including steel, stainless steel, and aluminum.
- Strong Welds: Produces robust and durable joints, especially in thicker materials.
- Cost-Effective: Equipment and consumables are generally less expensive compared to more advanced methods like laser welding.
- Automation Compatibility: Easily integrated into robotic systems for industrial-scale production.
Limitations and Challenges of MIG Welding
While MIG welding is highly versatile, it does have some limitations:
- Spatter Production: MIG welding often produces more spatter than precision methods like laser welding, requiring additional cleanup.
- Heat Input: The process generates significant heat, which can cause warping or distortion in thin materials.
- Shielding Gas Dependency: Outdoor welding can be challenging as shielding gas can be disrupted by wind.
- Weld Appearance: Without proper technique, MIG welds may not have the clean, aesthetic finish achieved with other methods.
- Thickness Limitation for Automation: Although effective for thick metals, automated MIG welding can struggle with precision in very thin materials.
Applications of MIG Welding
MIG welding is a versatile process widely used across various industries for diverse applications:
- Automotive Industry: Used for bodywork, frames, and structural components due to its speed and efficiency.
- Construction and Infrastructure: Ideal for fabricating steel beams, pipelines, and heavy machinery.
- Aerospace: Though less common than laser welding, MIG is used for structural components in aircraft and space vehicles.
- Shipbuilding: Effective for joining steel and aluminum panels in ship hulls and other marine structures.
- General Fabrication: Frequently used in manufacturing furniture, appliances, and other metal products.
Head-to-Head Comparison: Laser Welding VS MIG Welding
Heat Input and Distortion
- Laser Welding: Employs a highly focused laser beam that minimizes heat input and creates a small heat-affected zone (HAZ). This results in minimal distortion, making it suitable for thin or precision parts.
- MIG Welding: Produces a larger HAZ due to greater heat input, often leading to warping or distortion, particularly in thinner materials.
Welding Speed
- Laser Welding: Delivers exceptionally high welding speeds, especially in automated systems, boosting production rates in high-volume operations.
- MIG Welding: Slower compared to laser welding due to the continuous deposition of filler material and manual or semi-automatic operation.
Material Thickness and Weld Geometry
- Laser Welding: Ideal for thin to medium-thickness metals and precise geometries. For thicker materials, multiple passes or pre-weld preparations are often required.
- MIG Welding: Excels in welding thicker metals and accommodates less precise geometries, making it a versatile choice for general fabrication.
Metallurgical Quality
- Laser Welding: Produces high-quality welds with minimal porosity, contamination, or spatter, ensuring superior metallurgical integrity.
- MIG Welding: Delivers strong welds but is prone to defects such as porosity and spatter, which may require post-weld cleanup or additional inspection.
Joint Preparation and Fit-Up Requirements
- Laser Welding: Demands precise alignment and minimal gaps in joints due to the narrow focus of the laser beam. Tight tolerances are critical for success.
- MIG Welding: More forgiving with joint preparation, as the filler material can bridge gaps and compensate for imperfect fit-ups.
Use of Filler Materials
- Laser Welding: Often performed without filler material, relying on the melting of base materials. Filler can be used when needed but adds complexity to the process.
- MIG Welding: Consistently uses a wire electrode as filler, which is advantageous for bridging gaps or reinforcing welds.
Efficiency and Material Utilization
- Laser Welding: High material efficiency with minimal waste due to its precision and the non-contact nature of the process.
- MIG Welding: Higher material usage due to continuous filler wire consumption and spatter generation, leading to some material loss.
Equipment Complexity and Cost
- Laser Welding: Requires advanced equipment with high initial costs for lasers, optics, and automated systems. Best suited for industries with significant production needs and budgets.
- MIG Welding: Relatively simple and cost-effective equipment, making it accessible for small to medium-sized operations and general fabrication.
Skill Requirements and Operator Training
- Laser Welding: Requires specialized training for operators to handle advanced equipment and maintain precise parameters. Programming skills for automation are often necessary.
- MIG Welding: Easier to learn and operate, with minimal training required for basic proficiency. Ideal for manual and semi-automatic applications.
Maintenance and Downtime
- Laser Welding: Maintenance involves complex components such as lasers, optics, and cooling systems, resulting in higher costs and potential downtime.
- MIG Welding: Maintenance is straightforward, focusing on consumables like wire and tips, with lower costs and faster repair times.
Summary
Aspect | Laser Welding | MIG Welding |
Heat Input and Distortion | Low, minimal distortion | High, more distortion |
Welding Speed | Faster, highly productive | Slower in comparison |
Material Thickness | Best for thin-medium materials | Ideal for thicker materials |
Metallurgical Quality | High, minimal defects | Reliable but prone to defects |
Joint Preparation | Requires precise alignment | Forgiving, suitable for larger gaps |
Use of Filler Materials | Optional, adds complexity | Essential, bridges gaps |
Efficiency | High, minimal waste | Moderate, higher material usage |
Equipment Cost | Expensive, advanced technology | Affordable and accessible |
Skill Requirements | Specialized training required | Easy to learn, less training needed |
Maintenance | Complex, higher downtime | Simple, lower downtime |
Selecting the Right Process for Your Application
Material Thickness and Type
- Laser Welding: Best suited for thin to medium-thickness materials where precision and minimal heat input are critical. It excels in welding high-strength alloys, stainless steel, aluminum, and titanium, making it a preferred choice in aerospace, electronics, and medical device industries. Laser welding may face challenges with reflective materials like copper unless specialized lasers are used.
- MIG Welding: Performs well across a broad range of thicknesses, especially for thick metals and structural components. It is highly versatile for welding carbon steel, stainless steel, and aluminum. However, it struggles with intricate or delicate materials where distortion must be avoided.
Required Tolerances and Distortion Control
- Laser Welding: Provides unmatched precision and distortion control due to its concentrated heat source and small heat-affected zone (HAZ). It is ideal for applications requiring tight tolerances, intricate joint geometries, and high-quality finishes.
- MIG Welding: More forgiving in terms of joint fit-up and alignment but generates greater heat input, resulting in a larger HAZ and increased risk of distortion. It is better suited for projects where minor tolerances and heat-induced warping are acceptable.
Production Volume and Automation
- Laser Welding: Highly efficient for large-scale, high-volume production lines. Its speed and compatibility with robotic systems make it the optimal choice for automated manufacturing, especially in industries like automotive, where consistency and speed are critical.
- MIG Welding: While automation is possible, MIG welding is often used in manual or semi-automatic setups, making it suitable for low-to-medium production volumes. It is a cost-effective solution for custom fabrication, repairs, and smaller batches.
Budget and ROI Considerations
- Laser Welding: The initial investment in laser welding equipment is significantly higher due to the advanced technology required. However, for high-volume production or applications demanding precision, the long-term ROI is favorable because of reduced material waste, lower post-weld finishing costs, and faster production cycles.
- MIG Welding: The lower upfront cost of MIG welding equipment makes it accessible for smaller businesses or projects with limited budgets. However, increased material consumption (filler wire), higher energy usage, and post-weld cleanup may lead to higher operating costs in the long run.