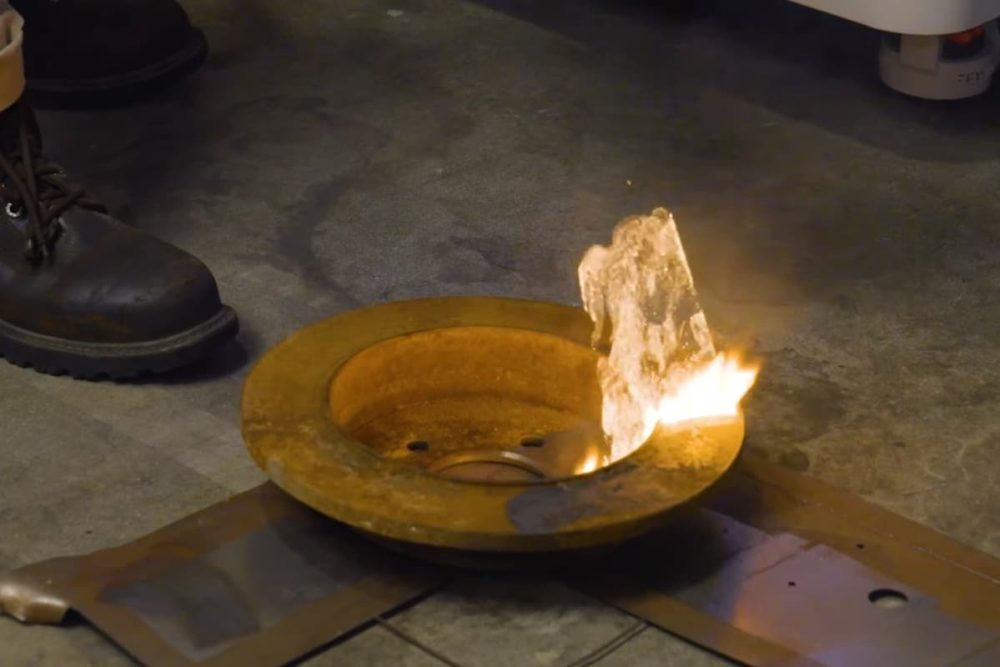
Understanding Rust and the Need for Removal
What is Rust?
Why Remove Rust?
Traditional Methods of Rust Removal
Rust removal has historically relied on techniques such as sandblasting, chemical treatments, and manual scraping or grinding:
- Sandblasting: This method uses high-pressure streams of abrasive particles to strip rust from surfaces. While effective on large, heavily corroded areas, it can be harsh on delicate components, generating significant dust and waste, and posing environmental and safety concerns.
- Chemical Treatments: Rust-removing chemicals dissolve corrosion through acidic or alkaline reactions. While useful for intricate parts, these treatments often involve hazardous substances, requiring careful handling and disposal.
- Manual Scraping or Grinding: This labor-intensive method involves using tools like wire brushes or grinders to physically remove rust. While cost-effective for small areas, it can be time-consuming and unsuitable for large-scale applications.
Sandblasting
What is Sandblasting?
Equipment and Setup
Sandblasting requires specialized equipment to achieve its desired effects. The key components include:
- Air Compressor: Generates the high-pressure air needed to propel the abrasive materials.
- Blasting Pot or Tank: Stores the abrasive media and feeds it into the blasting system.
- Blasting Hose and Nozzle: Directs the high-speed stream of abrasive material onto the target surface.
- Abrasive Media: The material used to clean or prepare the surface.
- Protective Gear: Includes helmets, gloves, goggles, and respiratory protection to ensure operator safety during the process.
Types of Abrasive Media
The effectiveness of sandblasting depends largely on the type of abrasive media used. Common options include:
- Silica Sand: A traditional choice for rust removal, though it produces hazardous silica dust.
- Aluminum Oxide: A durable, reusable abrasive for aggressive rust removal and surface profiling.
- Glass Beads: A gentler option that produces a smooth finish, ideal for softer or delicate surfaces.
- Steel Grit: Sharp and angular, designed for heavy-duty cleaning and rust removal.
- Soda (Baking Soda): Non-abrasive and safe for softer surfaces, minimizing damage.
- Walnut Shells or Corncob: Organic, eco-friendly options for light cleaning and polishing.
Advantages of Sandblasting
- Effective for Large-Scale Projects: Sandblasting efficiently removes rust, paint, and other coatings from large surfaces, making it a practical choice for industrial applications.
- Surface Preparation: The process creates a rough surface profile, enhancing the adhesion of primers, paints, and coatings.
- Versatility: Sandblasting can be used on various materials, including metals, wood, and concrete.
- High Speed: It can quickly clean and prepare large areas, saving time in comparison to manual methods.
Limitations and Drawbacks of Sandblasting
- Environmental and Health Concerns: Sandblasting produces significant dust and debris, which can pose serious health risks, especially from silica exposure, and requires proper containment to avoid environmental contamination.
- Potential Surface Damage: The abrasive action can damage delicate or intricate surfaces, making it unsuitable for precision tasks.
- Waste Generation: Many types of abrasive media cannot be reused, resulting in higher material costs and waste management requirements.
- High Equipment Maintenance: The wear and tear on blasting equipment requires regular maintenance, increasing operational costs.
- Limited Precision: Sandblasting lacks the control needed for targeted rust removal or delicate restoration projects.
Laser Cleaning
What is Laser Cleaning?
The Science Behind Laser Ablation
Equipment and Components
A laser cleaning system comprises the following components:
- Laser Source: Typically a fiber laser, chosen for its stability, efficiency, and ability to deliver high-energy pulses.
- Optical System: Includes lenses and mirrors to focus and direct the laser beam onto the target area.
- Handheld or Automated Cleaning Head: Used to apply the laser beam to the surface. This can be manually controlled or integrated into robotic systems for automated operations.
- Control Unit: Allows precise adjustment of laser parameters such as power, pulse frequency, and beam diameter to suit specific cleaning tasks.
- Fume Extraction System: Captures and filters vaporized particles, ensuring a safe and clean workspace.
Advantages of Laser Cleaning
- Non-Abrasive and Safe for Surfaces: Laser cleaning removes contaminants without harming the underlying material, making it ideal for delicate and high-precision applications.
- Environmentally Friendly: The process requires no chemicals, generates minimal waste, and avoids hazardous by-products, supporting sustainability efforts.
- Highly Precise: The laser can be targeted with pinpoint accuracy, making it suitable for complex shapes, small areas, or intricate details.
- Cost-Effective Over Time: Despite higher initial investment, the lack of consumables and minimal maintenance requirements reduce operating costs in the long term.
- Adaptability and Automation: The equipment can be customized for various materials and tasks and easily integrated into automated systems for large-scale or repetitive processes.
Limitations and Considerations
- Higher Initial Costs: The advanced technology and equipment used in laser cleaning come with a significant upfront investment compared to traditional methods like sandblasting.
- Slower on Large Surfaces: While precise, laser cleaning can be slower when removing rust from large areas, making it less time-efficient for such applications.
- Material-Specific Requirements: The effectiveness depends on the material being cleaned and the thickness of the contaminant layer, necessitating careful parameter tuning.
- Training and Expertise: Operators need specialized training to optimize the laser cleaning process and handle the equipment safely.
- Energy Consumption: Laser systems may require higher energy input, increasing operational costs for prolonged use.
Comparing Laser Rust Removal and Sandblasting
Mode of Action
- Laser Rust Removal: Laser cleaning employs a focused laser beam to vaporize rust and contaminants through a process called laser ablation. This method is precise and non-contact, targeting only the affected areas without damaging the underlying surface.
- Sandblasting: Sandblasting relies on high-pressure streams of abrasive media to physically remove rust, coatings, or contaminants. The abrasive materials impact the surface, stripping away rust along with a layer of the base material in some cases.
Resulting Surface Quality
- Laser Rust Removal: Leaves the surface clean and smooth, preserving the integrity of the base material. It is ideal for applications where the original texture or details of the metal must be maintained.
- Sandblasting: Produces a roughened surface that is suitable for priming and coating. However, it can cause micro-scratches or deformities, especially on softer metals or delicate parts.
Process Control and Selectivity
- Laser Rust Removal: Provides unparalleled control, allowing adjustments to laser power, frequency, and intensity for targeted rust removal. It is highly selective, making it suitable for intricate or sensitive surfaces.
- Sandblasting: Offers limited control and is less precise, often impacting the surrounding areas and base material along with the rust. It is better suited for large, uniform surfaces.
Health and Environmental Impact
- Laser Rust Removal: An eco-friendly solution that does not require abrasive media or chemicals. It generates minimal waste in the form of micro-particles, which are easily filtered, and eliminates the risk of airborne contaminants.
- Sandblasting: Produces significant dust and debris, which can include hazardous materials like silica, posing health risks such as respiratory issues. Sandblasting waste is often difficult to contain and may harm the environment.
Safety Considerations
- Laser Rust Removal: Requires operators to use protective eyewear to guard against laser exposure, but the process is otherwise safe and reduces physical risks due to its non-contact nature.
- Sandblasting: Involves greater safety risks, including exposure to high-velocity abrasive materials, airborne dust, and potential equipment malfunctions. Operators must wear full protective gear and respiratory equipment.
Cost and Economic Factors
- Laser Rust Removal: This has a higher upfront cost due to the advanced technology and equipment involved. However, its minimal consumables, low maintenance needs, and long-term efficiency can result in cost savings over time.
- Sandblasting: Offers lower initial costs but requires ongoing expenses for abrasive media, equipment maintenance, and waste management, making it less economical in the long run.
Mobility and Integration
- Laser Rust Removal: Compact and portable laser cleaning systems are easy to transport and integrate into automated production lines or robotic setups, offering high flexibility.
- Sandblasting: Typically requires a stationary setup with an air compressor, blasting pot, and containment systems, making it less mobile. Automation is possible but more complex and less adaptable than laser systems.
Scalability and Throughput
- Laser Rust Removal: Best suited for medium-scale tasks or applications requiring high precision. Cleaning large surfaces may take more time compared to abrasive methods.
- Sandblasting: Highly scalable for large-scale projects, as it can clean extensive areas quickly. However, it may not be practical for intricate or high-precision tasks.
Applications and Industry Perspectives
Manufacturing and Fabrication
Automotive and Transportation
Aerospace and Defense
Cultural Heritage and Restoration
Marine and Offshore Industries
Environmental and Regulatory Considerations
Abrasive Waste and Environmental Footprint
Health and Worker Safety
Compliance with Standards and Certifications
Both laser rust removal and sandblasting are subject to various industry standards and regulations aimed at ensuring environmental and worker safety.
- Laser Rust Removal aligns easily with stringent environmental and safety standards due to its clean and sustainable operation. It is often certified for use in industries with strict guidelines, such as aerospace, automotive, and cultural heritage preservation. Additionally, the reduced waste and absence of hazardous chemicals simplify compliance with environmental protection laws.
- Sandblasting, while effective, faces increasing scrutiny from regulatory bodies due to its environmental impact and health risks. In many regions, the use of silica sand is banned or heavily regulated to prevent occupational illnesses. Companies must adhere to strict waste disposal practices and ensure proper ventilation and protective measures, adding complexity to compliance efforts. Certifications for sandblasting operations often involve meeting specific safety and environmental criteria, which can be costly and time-consuming.
Economic and Operational Analysis
Return on Investment (ROI)
The economic efficiency of rust removal methods depends largely on the initial investment, operating costs, and long-term benefits.
- Laser Rust Removal: Though the upfront cost of laser cleaning equipment is higher, the long-term savings justify the investment for many industries. With no consumables like abrasive media and minimal maintenance needs, operational costs are significantly lower. The precision and material preservation of laser cleaning reduce waste, rework, and replacement costs, leading to a higher ROI over time. Moreover, the ability to integrate laser cleaning into automated production lines further enhances productivity, adding to its financial advantage.
- Sandblasting: The initial cost of sandblasting equipment is lower compared to laser systems. However, recurring expenses for abrasive media, waste disposal, and frequent maintenance can erode the cost advantage. For high-throughput applications, the speed of sandblasting can provide a good short-term ROI, but industries must factor in long-term costs like material wear and environmental compliance.
Maintenance and Downtime
- Laser Rust Removal: Laser cleaning systems have minimal moving parts, leading to low maintenance requirements and increased reliability. Downtime is rare, and when maintenance is needed, it is typically straightforward and cost-effective. This makes laser cleaning a dependable option for operations requiring consistent uptime.
- Sandblasting: The abrasive nature of the process causes significant wear and tear on equipment, including hoses, nozzles, and compressors. Frequent maintenance and part replacements are necessary, leading to more downtime and increased operational costs. Additionally, setting up containment systems to manage dust and debris can be time-consuming, further affecting productivity.
Scalability and Flexibility
- Laser Rust Removal: Laser cleaning offers unparalleled flexibility. Systems can be scaled to suit small, intricate tasks or integrated into fully automated production lines for large-scale operations. Portable laser cleaning units provide additional versatility for on-site applications. Its ability to adapt to diverse materials and precision tasks makes it an ideal choice for industries with varied cleaning needs.
- Sandblasting: Sandblasting excels in scalability for large-scale rust removal projects. It is particularly efficient for cleaning extensive areas, such as ship hulls or industrial structures. However, it lacks the precision needed for intricate or delicate work and is less adaptable to automation compared to laser systems.
Training and Skill Requirements
- Laser Rust Removal: While laser systems are user-friendly, operators need specialized training to optimize laser parameters and ensure safety. However, the learning curve is relatively short, and once trained, operators can achieve consistent, high-quality results with minimal supervision. Additionally, advanced software and intuitive interfaces make modern laser systems easier to operate.
- Sandblasting: Sandblasting requires less technical expertise but demands physical effort and strict adherence to safety protocols. Operators must be skilled in handling high-pressure equipment and trained to use protective gear effectively to minimize risks. The need for extensive safety measures and labor-intensive operations can make sandblasting less efficient in terms of manpower.
Making the Decision
Scale and Throughput Requirements
- Laser Rust Removal: Best suited for small to medium-scale operations or tasks requiring high precision. While it can handle large areas, the process may be slower compared to sandblasting, making it ideal for industries prioritizing quality over sheer speed.
- Sandblasting: Excels in large-scale projects requiring high throughput, such as cleaning industrial machinery, ship hulls, or large infrastructure. Its rapid surface coverage makes it the preferred choice for extensive rust removal.
Material Sensitivity and Precision
- Laser Rust Removal: The non-abrasive and contact-free nature of laser cleaning makes it ideal for sensitive materials, intricate components, and high-value assets. Industries like aerospace, automotive, and cultural heritage restoration benefit greatly from its precision and ability to preserve base materials.
- Sandblasting: The abrasive action is less suitable for delicate or intricate surfaces, as it can cause damage or micro-scratches. It is better suited for rugged applications where surface texturing is acceptable or desired.
Long-Term Costs and ROI
- Laser Rust Removal: Higher upfront costs are offset by low operating expenses, reduced maintenance, and the elimination of consumables like abrasive media. Over time, these advantages result in a strong ROI, especially for businesses prioritizing sustainability and operational efficiency.
- Sandblasting: Initial costs are lower, but recurring expenses for abrasives, equipment maintenance, and waste disposal can add up. It remains cost-effective for short-term or high-volume projects, though long-term ROI may be less favorable compared to laser cleaning.
Environmental and Health Regulations
- Laser Rust Removal: Complies easily with modern environmental and health regulations. It generates minimal waste, produces no hazardous dust, and eliminates the need for abrasive media or chemicals. This makes it a sustainable choice for industries with strict regulatory requirements.
- Sandblasting: Generates significant waste and airborne dust, which can pose environmental and health hazards. Compliance with regulations often requires investment in containment systems, proper disposal practices, and enhanced worker safety protocols.
Integration with Automation and Industry 4.0
- Laser Rust Removal: Perfectly aligned with Industry 4.0 principles, laser systems can be seamlessly integrated into automated workflows, robotic arms, and smart manufacturing systems. This capability enhances productivity, consistency, and adaptability in advanced manufacturing environments.
- Sandblasting: While automation is possible, it is more complex and less adaptable compared to laser systems. Sandblasting setups are often manual or semi-automated, limiting their compatibility with modern smart manufacturing processes.
Training and Workforce Skills
- Laser Rust Removal: Requires specialized training to operate safely and efficiently. However, modern systems feature user-friendly interfaces, and the learning curve is relatively short. Once trained, operators can achieve precise, repeatable results with minimal supervision.
- Sandblasting: Less technical but more labor-intensive, sandblasting requires operators to be skilled in equipment handling and safety protocols. The process also involves wearing extensive protective gear, which can impact workforce efficiency and comfort.
When deciding between laser rust removal and sandblasting, consider the specific needs of your operation:
- Choose Laser Rust Removal if your priorities include precision, material preservation, environmental sustainability, and integration with advanced manufacturing systems. It is ideal for industries where quality and compliance are paramount, despite higher initial costs.
- Choose Sandblasting if your focus is on large-scale, high-throughput applications where speed and cost-effectiveness are key, and where surface texturing is acceptable.