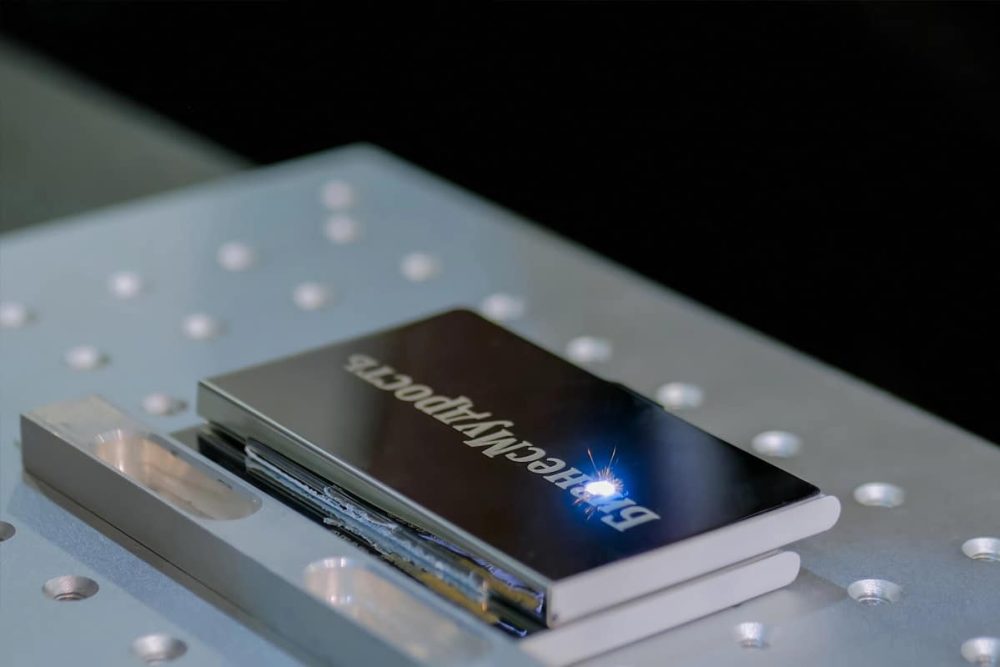
Laser Marking VS Screen Printing
In the world of product labeling and marking, choosing the right method is crucial for businesses aiming to maintain durability, precision, and cost efficiency. Two popular marking technologies—laser marking and screen printing—offer distinct advantages and applications, making the decision a significant one depending on specific industry needs. While screen printing has long been a go-to solution for its affordability and ability to produce vibrant designs, laser marking is emerging as a highly advanced alternative, delivering superior precision, permanence, and eco-friendliness.
This article explores the key differences between laser marking and screen printing, examining their processes, benefits, limitations, and suitable use cases. Whether your business prioritizes durability and precision or seeks a method optimized for high-volume production with colorful visuals, understanding these technologies will help you make an informed decision. By the end, you’ll be equipped to evaluate which marking method aligns with your operational goals and market demands.
Table of Contents
Overview of Laser Marking
What Is Laser Marking?
Laser marking is a precise and versatile technique that creates permanent marks on a variety of materials, including metals, plastics, ceramics, and glass. Using a concentrated laser beam, this non-contact method modifies the surface of the material to produce detailed and durable designs. Commonly used for applications such as serial numbers, barcodes, logos, and QR codes, laser marking is renowned for its ability to produce high-quality results with minimal environmental impact. Industries such as manufacturing, automotive, electronics, and medical devices rely on laser marking for its reliability and precision.
How Laser Marking Works
Laser marking uses a high-intensity laser beam that interacts with the surface of a material to create marks. This process does not require inks, chemicals, or physical contact, making it efficient and clean. There are several methods of laser marking, including:
- Annealing: Oxidizes the surface to create smooth, colorful, and heat-resistant marks, primarily on metals.
- Engraving: Removes layers of material to produce deep, tactile marks.
- Foaming: Creates raised, contrasting marks on plastics by forming bubbles within the material.
- Carbonizing: Reduces material oxygen content, resulting in darkened marks for higher contrast.
Each method caters to specific material properties and application requirements, offering exceptional versatility and precision.
Advantages of Laser Marking
- Durability: Laser marks are resistant to wear, fading, and environmental factors such as heat and chemicals, ensuring longevity.
- High Precision: Allows for intricate designs and detailed markings, ideal for small components like microchips or medical tools.
- Eco-Friendly: Operates without inks, solvents, or consumables, reducing waste and environmental impact.
- Versatility: Capable of marking a wide range of materials and shapes, from flat surfaces to curved objects.
- Cost-Effectiveness: While upfront costs are high, operational costs are low due to minimal maintenance and the absence of consumables.
- Speed: Supports high-speed marking, making it ideal for mass production.
Disadvantages of Laser Marking
- Initial Investment: Laser marking equipment requires a substantial upfront investment.
- Material Limitations: Certain reflective or transparent materials may need additional processing or specialized systems.
- Technical Expertise: Operators may require specialized training to handle the equipment and optimize results.
- Maintenance Needs: Periodic maintenance is necessary to ensure consistent performance over time.
Despite its disadvantages, laser marking is a leading technology for permanent and precise marking, offering significant advantages in durability, precision, and environmental sustainability. Its growing adoption reflects its effectiveness across a wide range of industrial applications.
Overview of Screen Printing
What Is Screen Printing?
Screen printing, also known as silk screening, is a time-tested printing technique used to apply designs, logos, or patterns onto a variety of materials, including textiles, plastics, glass, metal, and wood. The process involves transferring ink through a mesh screen onto the desired surface, using a stencil to define the design. Renowned for its ability to produce bold and vibrant prints, screen printing is widely employed in industries such as apparel, signage, packaging, and promotional products. Its affordability and visual impact make it a popular choice for mass production.
How Screen Printing Works
The screen printing process typically consists of these steps:
- Design Preparation: A stencil of the desired design is created and applied to a mesh screen. The stencil determines the areas where the ink will pass through.
- Screen Setup: The prepared screen is positioned over the material to be printed.
- Ink Application: Ink is spread across the screen using a squeegee, forcing it through the open areas of the stencil and onto the material.
- Curing: The printed design is heated or UV-cured to ensure the ink sets and adheres to the material.
For multi-colored designs, separate screens are prepared for each color, requiring precise alignment during printing. This method is ideal for both small designs and large, bold graphics.
Advantages of Screen Printing
- Vivid and Durable Prints: Produces bold, high-opacity colors that stand out, especially on dark surfaces, with strong resistance to wear and fading.
- Versatility: Can be applied to a wide range of materials and surfaces, including flat, curved, and flexible items.
- Cost-Effective for High Volumes: Economical for large-scale production, as setup costs are distributed across higher quantities.
- Texture and Depth: The thick ink layers create a textured, professional-quality finish that enhances visual appeal.
- Customizable Designs: Allows for creative, high-impact designs in a variety of sizes and formats.
Disadvantages of Screen Printing
- High Setup Costs: Preparing screens and stencils is labor-intensive and costly, making it less suitable for small production runs.
- Limited Detail and Precision: Fine details and complex designs are difficult to achieve compared to other methods, such as laser marking.
- Environmental Concerns: The process involves inks, solvents, and water for cleaning screens, which can generate waste and pollutants.
- Time-Consuming Preparation: Each new design or color requires a separate screen, adding to the preparation time.
- Not Ideal for Certain Materials: Struggles with uneven or highly textured surfaces, where ink application can be inconsistent.
Screen printing continues to be a preferred choice for large-scale, colorful designs thanks to its affordability and bold results. However, businesses must carefully evaluate its limitations, especially for intricate designs or projects requiring small runs or high precision.
Comparison Between Laser Marking and Screen Printing
Substrate Considerations
- Laser Marking: Laser marking is highly versatile, working on a wide range of materials, including metals, plastics, ceramics, glass, and even coated surfaces. Its non-contact process allows for marking irregular, curved, or delicate surfaces without damaging the material. However, reflective and transparent materials may require additional adjustments or specialized systems.
- Screen Printing: Screen printing works well on flat or slightly curved surfaces and is widely used on textiles, paper, plastic, glass, and wood. However, it struggles with highly textured, uneven, or irregularly shaped substrates, limiting its applicability in certain industries.
Quality and Durability
- Laser Marking: Laser marking creates permanent marks that are highly resistant to wear, fading, heat, and chemical exposure. This makes it ideal for applications where durability and longevity are essential, such as in automotive or medical devices.
- Screen Printing: Screen-printed designs are durable but can degrade over time, particularly when exposed to friction, UV light, or harsh environmental conditions. Its longevity depends on the type of ink and substrate used.
Production Speed and Efficiency
- Laser Marking: Laser marking is fast and efficient, especially for repetitive tasks in automated environments. Once programmed, it eliminates the need for additional setups, making it ideal for high-volume production.
- Screen Printing: Screen printing can produce large quantities quickly after the initial setup. However, the preparation of screens and stencils for each design or color is time-consuming, reducing efficiency for short or varied production runs.
Costs, Consumables, and Long-Term Investment
- Laser Marking: The upfront cost of laser marking equipment is significant, but the lack of consumables like ink or screens and minimal maintenance requirements result in low operational costs over time. It is a cost-effective solution for long-term production.
- Screen Printing: Screen printing has lower initial setup costs but requires ongoing expenses for inks, stencils, and cleaning materials. While economical for small runs, these recurring costs add up in large-scale or long-term applications.
Environmental Considerations
- Laser Marking: Laser marking is environmentally friendly, as it does not use inks, solvents, or water, and generates minimal waste. This makes it a sustainable option for businesses aiming to reduce their environmental footprint.
- Screen Printing: Screen printing generates waste from inks, solvents, and cleaning processes. Additionally, it consumes water and energy during setup and curing, resulting in a higher environmental impact compared to laser marking.
Safety Considerations
- Laser Marking: Safety measures are required to protect operators from laser radiation and fumes generated during marking. Proper training and equipment, such as protective enclosures and ventilation, ensure safe operation.
- Screen Printing: Screen printing involves handling potentially hazardous inks and chemicals, which require careful storage, ventilation, and protective gear to mitigate risks to operators.
Industry Applications
- Laser Marking: Laser marking is widely used in industries such as automotive, aerospace, medical devices, and electronics. Its precision and durability make it suitable for marking serial numbers, barcodes, QR codes, and intricate designs.
- Screen Printing: Screen printing is commonly used in textiles, signage, packaging, and promotional products. It is ideal for decorative and branding purposes, particularly for bold, colorful designs on fabrics, plastics, and glass.
Integrating Technology and Automation
- Laser Marking: Laser marking integrates seamlessly with automated production lines, supporting Industry 4.0 initiatives. It is highly programmable and compatible with real-time data monitoring, remote operation, and advanced quality control systems.
- Screen Printing: While screen printing can be partially automated, it still requires significant manual intervention for setup and design changes. Its scalability in highly automated environments is limited.
Quality Control and Traceability
- Laser Marking: Laser marking offers superior precision, making it ideal for traceable markings like barcodes, serial numbers, and micro text. Its ability to produce scannable and permanent marks ensures compliance with strict quality control standards.
- Screen Printing: Screen printing lacks the precision required for traceable markings. It is more suited for decorative or branding purposes, where traceability is not a primary concern.
Design Flexibility and Aesthetics
- Laser Marking: Laser marking delivers intricate, high-precision designs with sharp details. However, it is typically limited to monochromatic marks, with the color determined by the substrate material.
- Screen Printing: Screen printing excels in creating vibrant, multi-colored designs with a textured, tactile finish. However, achieving fine details or complex patterns may be challenging compared to laser marking.
Laser marking and screen printing offer unique advantages, making them suitable for different applications. Laser marking is ideal for industries requiring precision, durability, and automation, while screen printing is better suited for high-impact, colorful designs in decorative and branding contexts. Businesses should carefully evaluate factors such as substrate type, production volume, budget, and specific application needs to select the most appropriate technology for their requirements.
Selecting the Right Method
When choosing between laser marking and screen printing, several factors come into play. Understanding the requirements of your project in terms of material, design, durability, production needs, and budget will help determine the most suitable marking method.
Material and Substrate
- Laser Marking: Laser marking is highly adaptable to a variety of materials, including metals, plastics, ceramics, and glass. Its non-contact process enables it to mark curved, irregular, or delicate surfaces without causing damage. If your project involves challenging substrates or high-precision requirements, laser marking is the ideal choice.
- Screen Printing: Screen printing is effective for flat or slightly curved surfaces and works well with textiles, paper, plastics, and glass. However, it is less effective on complex or irregularly shaped materials and may not perform well on heat-sensitive substrates due to the curing process.
Design Complexity
- Laser Marking: For intricate designs, small text, barcodes, or detailed logos, laser marking provides unmatched precision and clarity. It is perfect for industries requiring high-detail work, such as medical devices and electronics.
- Screen Printing: Screen printing excels in bold, colorful designs with a textured finish. However, it struggles with fine details, especially in small or intricate patterns. This makes it more suitable for large, visually impactful designs.
Durability Requirements
- Laser Marking: Laser marking produces permanent, wear-resistant markings that can withstand harsh conditions, including abrasion, UV exposure, chemicals, and extreme temperatures. It is the preferred choice for industries where long-term durability is crucial, such as automotive, aerospace, and manufacturing.
- Screen Printing: While screen-printed designs are durable under standard conditions, they are more prone to fading, scratching, or deterioration when exposed to repeated wear or environmental factors. It is best suited for applications where longevity is not the primary concern.
Volume and Frequency of Design Changes
- Laser Marking: Laser marking is highly efficient for high-volume production and offers flexibility for frequent design changes. Since the process is digitally controlled, new designs can be implemented quickly without the need for physical screens or stencils.
- Screen Printing: Screen printing is cost-effective for large batches of the same design but becomes time-intensive and expensive for frequent changes. Each new design or color requires creating and preparing new screens, making it less practical for dynamic production needs.
Budget and ROI
- Laser Marking: While laser marking involves a higher initial investment, its long-term cost savings are significant due to the absence of consumables like inks or screens and minimal maintenance requirements. For businesses focused on ROI and scalable production, laser marking is a worthwhile investment.
- Screen Printing: Screen printing has a lower upfront cost, making it more accessible for smaller projects or businesses with limited budgets. However, recurring expenses for consumables and equipment maintenance can add up, reducing its cost-effectiveness for high-volume or long-term applications.
Selecting the right marking method depends on the specific needs of your application. Laser marking is ideal for businesses prioritizing precision, durability, and flexibility, particularly in high-volume or automated settings. Screen printing, on the other hand, is a better fit for projects requiring bold, colorful designs at a lower initial cost. By considering factors such as material, design complexity, durability, production frequency, and budget, you can choose the most effective solution for your marking requirements.
Summary
When comparing laser marking and screen printing, each technology offers unique advantages and caters to different needs. Laser marking stands out for its precision, durability, and versatility, making it ideal for industries that require permanent, high-quality markings on various materials such as metals, plastics, and ceramics. Its non-contact process ensures minimal waste and is environmentally friendly, with no need for consumables like ink or chemicals. While the upfront cost is higher, its long-term cost-effectiveness and compatibility with automation make it an excellent choice for businesses focused on scalability and efficiency.
Screen printing, on the other hand, is renowned for producing vibrant, colorful designs with a textured finish. It is highly suitable for applications such as textiles, packaging, and promotional products, especially when large quantities of identical designs are required. However, it struggles with fine details, complex designs, and frequent design changes.
Ultimately, selecting the right method depends on your material, design complexity, durability needs, production volume, and budget. Both methods have their strengths, and understanding these factors ensures an informed decision tailored to your specific requirements.