Introduction
Sheet Laser Cutting Machines
-
VIF-A Laser Cutting Machine
Rated 4.50 out of 5$12,500.00 – $34,000.00 Select options This product has multiple variants. The options may be chosen on the product page -
VIF Laser Cutting Machine
Rated 4.75 out of 5$17,300.00 – $70,000.00 Select options This product has multiple variants. The options may be chosen on the product page -
VIE Laser Cutting Machine
Rated 5.00 out of 5$21,800.00 – $166,500.00 Select options This product has multiple variants. The options may be chosen on the product page -
VIB Laser Cutting Machine
Rated 5.00 out of 5$21,300.00 – $166,000.00 Select options This product has multiple variants. The options may be chosen on the product page -
VIP Laser Cutting Machine
Rated 4.75 out of 5$25,800.00 – $170,500.00 Select options This product has multiple variants. The options may be chosen on the product page -
VIH Laser Cutting Machine
Rated 4.75 out of 5$92,000.00 – $420,000.00 Select options This product has multiple variants. The options may be chosen on the product page
Applications
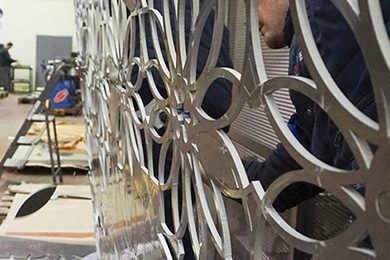
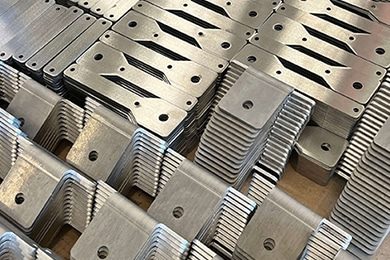

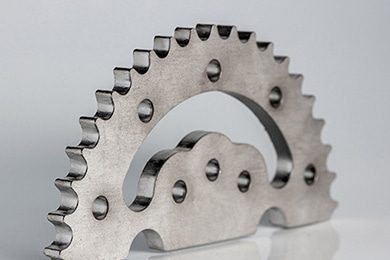
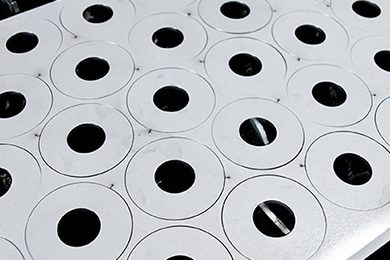
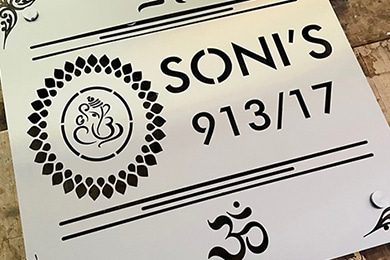
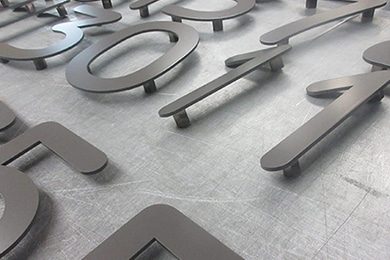
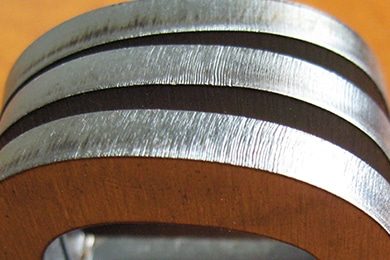
Advantages of Sheet Laser Cutting
High Precision and Accuracy
Sheet laser cutting provides exceptional precision, capable of creating intricate designs and fine details with minimal deviation, ensuring that every cut meets exact specifications without the need for further machining.
Minimal Material Waste
Laser cutting maximizes material usage by producing clean, precise cuts with minimal kerf, reducing scrap and lowering material costs, which makes it highly efficient for both small and large production runs.
Fast Processing Speed
With rapid cutting capabilities, sheet laser cutting machines significantly increase production speed. This efficiency allows for faster turnaround times and greater throughput, even for complex designs or thicker materials.
Versatility Across Materials
Laser cutting is compatible with a wide variety of materials, including carbon steel, stainless steel, aluminum, copper, and brass, allowing manufacturers to tackle diverse projects without the need for multiple machines or complex setups.
Clean and Smooth Edges
Laser cutting results in clean, smooth edges with minimal heat-affected zones, reducing the need for post-processing work such as deburring, which ultimately saves time and labor costs.
Minimal Tool Wear
Since lasers don’t make physical contact with the material, there is no tool wear, reducing maintenance costs and ensuring consistent performance over time without the need for frequent tool replacements.
Comparison with Other Cutting Methods
Cutting Method | Fiber Laser Cutting | Plasma Cutting | Waterjet Cutting | Flame Cutting |
Precision | Very High (±0.05 mm) | Moderate (±0.5 mm) | High (±0.1 mm) | Low (±1 mm) |
Material Compatibility | Metals (steel, aluminum, brass, copper) | Metals (mainly conductive, such as steel, aluminum, and brass) | Metals, plastics, glass, stone, ceramics, composites | Metals (primarily thicker materials like steel, and iron) |
Cutting Speed | Very Fast (high throughput) | Fast to Moderate | Moderate | Slow |
Edge Quality | Excellent (smooth edges, minimal burr) | Rough (requires post-finishing) | Smooth, minimal burr | Rough (requires post-finishing) |
Heat Affected Zone (HAZ) | Minimal (low distortion) | Moderate (significant distortion) | Minimal (low distortion) | High (significant distortion) |
Material Thickness | Thin to medium thickness (up to 50mm) | Medium to thick (up to 150mm) | Thin to thick (up to 200mm) | Thick (up to 300mm) |
Cost Efficiency | High (low material waste, minimal operational cost) | Medium (higher waste, higher operational cost) | Medium (high operational costs due to abrasives) | Low (low operational costs) |
Maintenance Needs | Low (minimal parts wear) | Medium (higher maintenance, consumable parts) | High (frequent maintenance) | High (frequent nozzle replacement) |
Environmental Impact | Low (energy-efficient, low material waste) | Moderate (gas emissions, noise) | High (water usage, waste disposal) | Moderate (gas emissions) |
Customer Reviews
Frequently Asked Questions
What Is The Sheet Laser Cutting Machine?
- Laser Source: The machine typically uses a fiber laser source to generate the laser beam. Fiber lasers are preferred for their efficiency, energy-saving capabilities, and ability to deliver highly focused beams for fine cuts, especially on metals like steel, aluminum, and brass.
- Cutting Bed: The flat surface or worktable where the sheet material is placed during the cutting process. It may include fixtures or clamps to hold the material securely in place, ensuring consistent accuracy throughout the operation.
- Control System: A combination of software and hardware that directs the cutting process. The control system allows operators to input design specifications, adjust settings in real-time, and fine-tune the operation for maximum precision.
- Cooling System: A vital feature to ensure that the laser generator and other critical components stay at optimal operating temperatures. It prevents overheating and ensures that the machine performs consistently, even during extended periods of use.
- Automation Options: Many modern sheet laser cutting machines come with automation features, such as automatic loading and unloading systems, which streamline the process, reduce manual labor, and increase throughput. These features enhance productivity and minimize human error.
How Much Does The Sheet Laser Cutting Machine Cost?
- Entry-Level Machines
- Price Range: $20,000 to $50,000
- Description: These models are designed for smaller-scale operations, hobbyists, or businesses just starting with laser cutting. They are typically less powerful, with smaller cutting areas and fewer advanced features. These machines are ideal for lighter materials and lower production volumes.
- Mid-Range Machines
- Price Range: $50,000 to $100,000
- Description: Mid-range machines offer enhanced performance, including better precision, larger cutting areas, and higher cutting speeds. They may also feature more advanced automation options, making them suitable for moderate production volumes and businesses looking to improve efficiency and output quality.
- High-End Machines
- Price Range: $100,000 to $500,000+
- Description: High-end laser cutting machines are equipped with advanced features such as high precision, high-speed capabilities, and large working areas. These machines are ideal for industries that require complex cuts, such as aerospace, automotive, and heavy manufacturing. They also often include cutting-edge automation systems for maximum productivity.
- Custom and Specialized Machines
- Price Range: $500,000+
- Description: Custom-built machines or those with specialized features, such as very high-power outputs, additional capabilities (e.g., 3D cutting), or specific design modifications, can exceed $500,000. These machines are typically tailored to meet the specific needs of large-scale, high-demand industries.
What Software Does The Sheet Laser Cutting Machine Use?
- Cypcut: Cypcut is a well-respected software known for its user-friendly interface and advanced cutting optimization features, perfect for industries where material usage is critical.
- Weihong: Weihong laser cutting system is another reliable software solution that excels in providing reliable control and real-time feedback, providing ease of use for a variety of applications.
How Precise Are The Cuts Achieved With A Sheet Laser-Cutting Machine?
- Cutting Tolerance: Laser cutting machines can achieve a cutting tolerance of ±0.1 mm to ±0.2 mm. This level of tolerance is suitable for most standard cutting tasks and ensures that parts are cut with minimal deviation from the desired design.
- Edge Quality: Laser cutting produces clean, smooth edges with minimal burrs or deformation. The edge quality is often very close to the theoretical dimensions of the design, ensuring that the final product requires little to no post-processing or finishing.
- Accuracy: The positional accuracy of modern laser cutting machines can be as precise as ±0.05 mm. This high degree of accuracy makes it possible to cut intricate and detailed designs with remarkable precision, even on small or complex components.
- Repeatability: High-quality laser cutting machines offer excellent repeatability, meaning they can consistently produce identical cuts with minimal variation. This makes laser cutting ideal for high-volume production runs where consistency is paramount.
What Are The Disadvantages Of The Sheet Laser Cutting Machine?
- High Initial Cost: The initial purchase price of a sheet laser cutting machine can be significant, especially for high-performance models. This can be a substantial investment for businesses, particularly small to medium-sized enterprises, making it important to carefully evaluate the long-term benefits versus the upfront cost.
- Maintenance Costs: Regular maintenance and occasional repairs can be costly, particularly for high-end or complex laser-cutting machines. Components such as laser heads, lenses, and mechanical parts may require replacement or servicing, adding to ongoing operating costs.
- Material Thickness Limitations: Although laser cutting is highly versatile, it may struggle with cutting very thick materials (e.g., metals beyond 50-100 mm) compared to other cutting methods like plasma or waterjet cutting. For materials with greater thicknesses, alternative methods may be more effective.
- Material Waste: Despite the precision of laser cutting, material waste can still occur, especially when dealing with irregularly shaped or small parts. The arrangement of parts on the sheet (nesting) plays a crucial role in minimizing waste, but this is often influenced by the design and the machine’s capabilities.
- Energy Consumption: Laser-cutting machines can consume significant amounts of energy, particularly during high-speed cutting or when working with thick materials. This can contribute to higher operational costs and may have an impact on energy efficiency, especially for large-scale operations.
- Heat-Affected Zones: The laser-cutting process generates heat, which can lead to thermal distortion or affect the material’s properties, particularly when cutting thin or sensitive materials. The heat-affected zone (HAZ) can impact the surface finish and mechanical properties of the material, requiring additional post-processing in some cases.
- Complex Setup: Setting up and calibrating a laser cutting machine for different materials, thicknesses, and cutting profiles can be complex and time-consuming. Operators must adjust cutting parameters such as speed, power, and focus, which can take time and require expertise, especially when switching between materials or cutting tasks.
- Skill Requirement: Operating and programming a laser cutting machine requires specialized training and skills. These machines are often more complex than traditional cutting methods, and operators must understand both the hardware and software to optimize performance. Lack of proper training can lead to inefficiencies, errors, or even damage to the machine.
How To Maintain The Sheet Laser Cutting Machine?
- Regular Cleaning
- Laser Lens and Mirrors: Clean the laser lens and mirrors regularly to remove dust, debris, and contaminants. Dirty optics can degrade beam quality and affect cutting precision.
- Work Area: Keep the work area clean by removing metal scraps, dust, and other debris that can interfere with the cutting process or damage the machine.
- Inspect and Replace Consumables
- Nozzles and Tips: Regularly inspect and replace nozzles, tips, and other consumables that can wear out with use, ensuring they are in good condition for precise cutting.
- Filters: Change air and water filters as recommended by the manufacturer to ensure efficient cooling, maintain air quality, and optimize laser cutting performance.
- Check Alignment and Calibration
- Beam Alignment: Ensure that the laser beam is aligned correctly. Misalignment can lead to reduced cutting precision and affect the quality of the finished product.
- Machine Calibration: Regularly calibrate the machine to maintain its accuracy and consistency. Proper calibration ensures that the machine performs at its highest level of precision.
- Lubrication
- Moving Parts: Lubricate rails, gears, and other moving parts to prevent wear and tear, ensuring smooth operation and reduced friction.
- Guides and Motors: Apply appropriate lubricants to guides and motors based on the manufacturer’s recommendations to keep them running efficiently.
- Cooling System Maintenance
- Cooling Fluids: Periodically check and replace cooling fluids to prevent overheating and maintain optimal performance of the laser generator.
- Cooling Fans: Ensure that cooling fans are clean and functioning properly. Replace them if necessary to ensure proper airflow and cooling during operation.
- Software and Firmware Updates
- Updates: Regularly update the software and firmware of your laser cutting machine to take advantage of the latest features, improvements, and bug fixes.
- Backup: Backup important settings and configurations to avoid data loss and ensure that the machine can be quickly restored if needed.
- Routine Inspections
- Structural Check: Perform regular inspections of the machine’s frame, bed, and other structural components to detect any signs of damage, cracks, or wear.
- Electrical Components: Inspect electrical connections and wiring for any signs of wear, loose connections, or overheating. Ensure that all electrical components are in good working condition.
- Follow the Manufacturer’s Guidelines
- Manual: Adhere to the maintenance schedule and guidelines outlined in the manufacturer’s manual. Follow the recommended intervals for cleaning, inspection, and replacement of components.
- Professional Service: Schedule regular professional servicing or inspections as recommended by the manufacturer. Certified technicians can provide in-depth checks and maintenance to ensure the machine is running optimally.
What Are The Operating Costs Of Sheet Laser Cutting Machines?
- Energy Consumption
- Electricity: Laser-cutting machines consume significant amounts of electricity, particularly machines with high-power laser generators. The energy consumption depends on the machine’s power rating and how many hours it operates daily. High-power systems typically use more electricity, leading to higher operational costs.
- Consumables
- Laser Gas: Sheet laser cutting machines require assist gases such as oxygen or nitrogen to facilitate cutting. The cost of these gases varies depending on the cutting process and material type, contributing to ongoing operational expenses.
- Nozzles and Lenses: Regular replacement of nozzles, lenses, and other consumables is necessary to maintain cut quality. These components degrade over time, especially during high-volume cutting operations, adding to the overall maintenance costs.
- Maintenance and Repairs
- Routine Maintenance: Regular maintenance such as cleaning, lubrication, and calibration is necessary to keep the machine running at its best. While preventive maintenance helps avoid costly breakdowns, it still incurs routine expenses.
- Repairs: Over time, repairs and the replacement of major components, such as the laser generator or motion systems, can be costly, particularly for high-end, complex machines.
- Material Costs
- Sheet Material: The cost of the materials being cut plays a significant role in the operating costs. Materials like stainless steel, aluminum, or copper may have higher costs, impacting overall operational budgets.
- Efficient Nesting and Cutting: By optimizing the cutting path and nesting (arranging pieces on the sheet material), material waste can be reduced. Waste management techniques help minimize costs.
- Cooling System
- Cooling Fluids: Maintaining an effective cooling system is vital to prevent overheating and ensure the machine’s longevity. The costs associated with cooling fluids and their regular replacement add to operational expenses.
- Electricity for Cooling: The cooling system also consumes additional electricity, further contributing to energy costs.
- Labor Costs
- Operator Wages: Trained operators or technicians are required to handle the machine, monitor cutting operations, and perform routine maintenance. Labor costs include wages, benefits, and any specialized training.
- Setup Time: Setup time for changing material, adjusting settings, or preparing a new cutting program adds to the labor costs, especially for complex cuts or custom jobs.
- Software and Licensing
- Software Costs: The cost of acquiring and maintaining design and control software for the machine is another ongoing expense. The software helps optimize cutting paths, improve material efficiency, and streamline operations.
- Licensing Fees: Some advanced software packages may require ongoing licensing fees, which add to the operating costs, especially in environments where software updates or features are continuously needed.
- Waste Disposal
- Scrap Management: Handling and disposing of metal scraps and other waste materials from the cutting process can incur additional costs. Efficient scrap management systems, which recycle or repurpose waste materials, can help minimize this expense.
What Is the Lifespan of Sheet Laser-Cutting Machines?
- Typical Lifespan
- 10 to 20 Years: Most sheet laser-cutting machines are designed to last between 10 to 20 years with proper maintenance and regular usage. This range is typical for many models that are used in industrial applications under normal operating conditions.
- High-Quality Machines
- Longer Lifespan: Higher-quality machines from reputable manufacturers often have extended lifespans, sometimes lasting over 20 years. These machines tend to have more durable components, better engineering, and more robust build quality, contributing to a longer useful life, especially when well-maintained.
- Factors Affecting Lifespan
- Usage: The frequency of use and the machine’s operational intensity can influence its lifespan. Machines that are used continuously or at maximum capacity may wear out faster, as high demand accelerates component fatigue.
- Maintenance: Regular maintenance is crucial for extending the machine’s life. Performing scheduled inspections, cleaning, and part replacements (like nozzles and lenses) helps prevent issues that can shorten the machine’s operational life.
- Operating Conditions: Environmental factors such as exposure to dust, temperature fluctuations, and humidity can affect the machine’s longevity. Machines in harsh or uncontrolled environments may experience more wear and tear.
- Technology and Upgrades
- Obsolescence: While a laser-cutting machine may still be operational after many years, technological advancements could make it obsolete. Newer models may offer better performance, faster cutting speeds, or more efficient energy use, prompting companies to upgrade their equipment even if the older machines are still functioning.
Related Resources
Laser Marking VS Screen Printing
Laser Welding VS MIG Welding
Laser Rust Removal VS Sandblasting Rust Removal
Fiber Laser Cutting VS Plasma Cutting
Contact Us
Contact Information Form: