Introduction
Fiber Laser Cutting Machines
-
VIF-A Laser Cutting Machine
Rated 4.50 out of 5$12,500.00 – $34,000.00 Select options This product has multiple variants. The options may be chosen on the product page -
VIF Laser Cutting Machine
Rated 4.75 out of 5$17,300.00 – $70,000.00 Select options This product has multiple variants. The options may be chosen on the product page -
VIE Laser Cutting Machine
Rated 5.00 out of 5$21,800.00 – $166,500.00 Select options This product has multiple variants. The options may be chosen on the product page -
VIB Laser Cutting Machine
Rated 5.00 out of 5$21,300.00 – $166,000.00 Select options This product has multiple variants. The options may be chosen on the product page -
VIP Laser Cutting Machine
Rated 4.75 out of 5$25,800.00 – $170,500.00 Select options This product has multiple variants. The options may be chosen on the product page -
VIH Laser Cutting Machine
Rated 4.75 out of 5$92,000.00 – $420,000.00 Select options This product has multiple variants. The options may be chosen on the product page -
VIF-T Laser Cutting Machine
Rated 4.75 out of 5$34,300.00 – $179,000.00 Select options This product has multiple variants. The options may be chosen on the product page -
VIE-T Laser Cutting Machine
Rated 4.75 out of 5$43,300.00 – $188,000.00 Select options This product has multiple variants. The options may be chosen on the product page -
VIP-T Laser Cutting Machine
Rated 5.00 out of 5$68,800.00 – $213,500.00 Select options This product has multiple variants. The options may be chosen on the product page -
VIT Laser Cutting Machine
Rated 4.75 out of 5$24,300.00 – $167,500.00 Select options This product has multiple variants. The options may be chosen on the product page -
VIT-A Laser Cutting Machine
Rated 5.00 out of 5$79,300.00 – $222,500.00 Select options This product has multiple variants. The options may be chosen on the product page
Applications
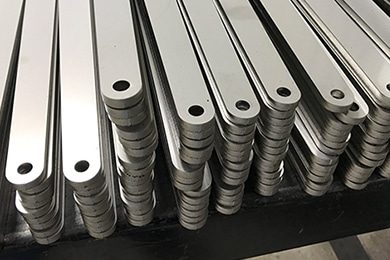
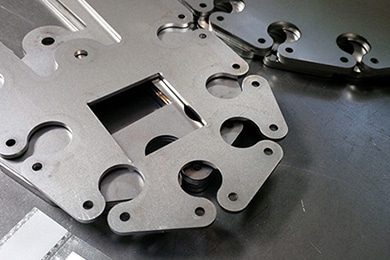
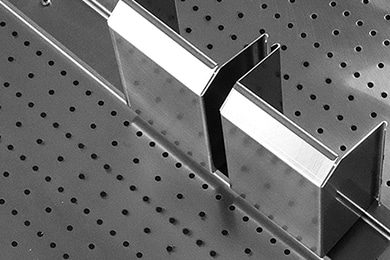
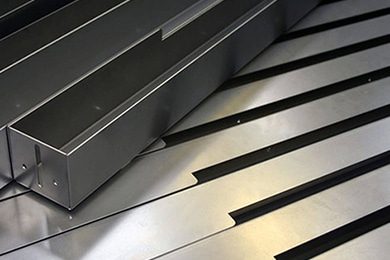
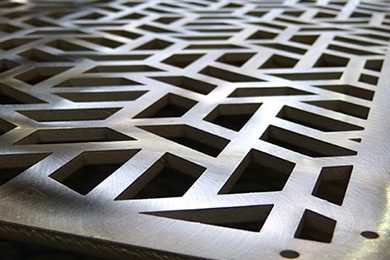
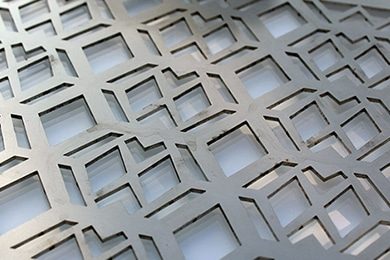
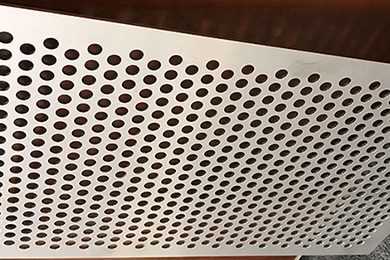
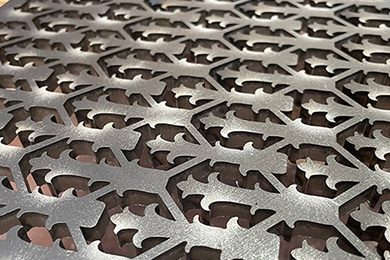
Advantages of Fiber Laser Cutting
High Precision and Accuracy
Fiber lasers produce exceptionally fine cuts with tight tolerances, ensuring high-quality results. Their ability to cut intricate shapes and patterns with minimal material waste makes them ideal for precision-driven applications.
Faster Cutting Speeds
Fiber laser cutting machines offer significantly faster cutting speeds compared to traditional methods, improving overall productivity. Their rapid processing time helps reduce cycle times, making them ideal for high-volume manufacturing.
Low Operational Costs
With higher energy efficiency and lower maintenance requirements, fiber laser cutting machines provide long-term cost savings. They consume less power, reducing operating costs and enhancing profitability over time.
Versatility in Material Handling
Fiber laser cutting machines can cut a wide range of materials, from thin sheets to thick plates. They are highly effective on metals like stainless steel, aluminum, brass, and copper, making them versatile for multiple industries.
Minimal Maintenance Requirements
Thanks to their solid-state design, fiber laser cutting machines require less maintenance than CO2 lasers. The absence of mirrors and other complex components reduces wear and tear, ensuring a longer machine lifespan and fewer service interruptions.
More Consistent Cuts
Fiber lasers produce cleaner, smoother edges with minimal slag or burrs, reducing the need for post-processing. This ensures higher-quality parts and a more efficient manufacturing process.
Comparison with Other Cutting Methods
Feature | Fiber Laser Cutting | Plasma Cutting | Waterjet Cutting | Flame Cutting |
Cutting Speed | Very high speed, especially on thinner materials | Moderate, slower than fiber lasers | Slow compared to laser and plasma | Slow, especially for thicker materials |
Precision | High precision with tight tolerances | Moderate precision | High precision, but not as fine as fiber laser | Lower precision, less control over cut quality |
Material Thickness | Best for thin to medium thicknesses (up to 25mm) | Effective for medium to thick materials (up to 100mm) | Effective for all thicknesses, but slower for thick cuts | Suitable for thick materials (up to 300mm) |
Material Types | Primarily metals (stainless steel, aluminum, etc.) | Primarily metals (stainless steel, aluminum, etc.) | Can cut metals, plastics, glass, ceramics, and composites | Primarily metals (steel, iron, etc.) |
Cut Quality | Clean, smooth cuts with minimal slag or burrs | Rougher cuts with more slag and oxidation | Clean, smooth cuts with minimal heat-affected zones | Rough cuts with more slag and distortion |
Heat Affected Zone (HAZ) | Minimal HAZ, no thermal distortion | Larger HAZ, potential distortion | Minimal HAZ, ideal for delicate materials | Large HAZ, leading to distortion and material changes |
Cost of Equipment | Higher initial cost but lower operational costs | Lower initial cost but higher operating costs | Moderate initial cost, high maintenance | Low initial cost but high operational costs |
Maintenance | Low maintenance, minimal parts wear | Higher maintenance, consumable parts (electrodes, nozzles) | Moderate maintenance, expensive consumables | High maintenance, often requires skilled labor |
Operational Cost | Low, energy-efficient with minimal consumables | Moderate, high energy consumption | High, water and abrasive consumables increase cost | High, fuel and oxygen costs add up quickly |
Environment Impact | Low, with minimal fumes or waste | Moderate, produces fumes and noise | Very low, produces no hazardous emissions | High, produces fumes, smoke, and pollutants |
Customer Reviews
Frequently Asked Questions
How Much Do Fiber Laser Cutting Machines Cost?
- Basic Fiber Laser Cutting Machines: $15,000 to $50,000. These machines typically feature lower power and fewer advanced features, making them ideal for small businesses or workshops looking for cost-effective cutting solutions.
- Mid-Range Fiber Laser Cutting Machines: $50,000 to $150,000. Offering higher power, greater precision, and additional features such as automatic loading and unloading systems, these machines cater to medium-sized businesses or industries with higher production needs.
- High-End Fiber Laser Cutting Machines: $150,000 to $300,000. These models are equipped with advanced features like high-power lasers, automated controls, and specialized cutting capabilities, making them suitable for large-scale operations that demand top-tier performance.
- Advanced Feature Fiber Laser Cutting Machines: Over $500,000. Machines in this category include state-of-the-art components, such as very high-power lasers, specialized cutting heads, and full automation for large-scale industrial applications. These are often custom solutions for specialized needs.
What Materials Can the Fiber Laser Cutting Machine Process?
- Carbon Steel: Fiber lasers are ideal for cutting carbon steel of varying thicknesses. The high precision and speed make them perfect for use in construction, manufacturing, and other industries requiring strong, reliable cuts.
- Stainless Steel: Stainless steel is easily processed by fiber lasers, which produce clean, smooth edges with minimal heat-affected zones. This is especially useful for applications like food processing equipment, medical devices, and decorative metalwork.
- Aluminum: Fiber lasers can cut aluminum effectively, although due to its reflective nature, they require higher power settings and specialized adjustments to ensure clean, burr-free cuts without damaging the equipment.
- Copper: Copper and its alloys, known for their high reflectivity and thermal conductivity, can be cut using fiber lasers with proper settings. Modern fiber lasers are designed to handle copper efficiently, providing precise cuts.
- Brass: Like copper, brass has reflective properties that demand careful handling. However, fiber lasers can achieve clean cuts in brass, making them ideal for a range of industrial and decorative applications.
- Titanium: Fiber lasers are highly effective in cutting titanium, a metal known for its strength and lightweight properties. This capability is essential in industries like aerospace and medical applications, where high-performance materials are crucial.
- Galvanized Steel: Fiber lasers can cut galvanized steel with ease, allowing for precise cuts through the zinc coating without damaging the material. This is especially useful in industries such as automotive, construction, and HVAC.
- Tool Steel: Tool steel, known for its hardness and wear resistance, can be cut with fiber lasers, which is crucial for producing tools and molds used in high-precision manufacturing.
- Nickel Alloys: Fiber lasers can process nickel alloys, which are often used in industries like aerospace and chemical processing. The high precision ensures clean cuts, even for these specialized, high-performance materials.
What Thicknesses Can the Fiber Laser Cutting Machine Cut?
- Carbon Steel
- Maximum Cutting Limit: 80mm
- Maximum Thickness for Batch Processing: 60mm
- Stainless Steel
- Maximum Cutting Limit: 50mm
- Maximum Thickness for Batch Processing: 40mm
- Aluminum Alloy
- Maximum Cutting Limit: 30mm
- Maximum Thickness for Batch Processing: 20mm
- Brass
- Maximum Cutting Limit: 18mm
- Maximum Thickness for Batch Processing: 15mm
- Copper
- Maximum Cutting Limit: 12mm
- Maximum Thickness for Batch Processing: 10mm
How to Choose Fiber Laser Cutting Machines?
- Material and Thickness: Identify the types of materials (e.g., carbon steel, stainless steel, aluminum, brass, copper) and their thicknesses that you will cut regularly. Choose a machine with sufficient power to efficiently handle these materials.
- Power and Speed: Higher power (e.g., 40kW) enables cutting through thicker materials and increases cutting speed. Consider a power level that balances your material needs and desired production speed.
- Cutting Area: Consider the maximum dimensions of the sheets or plates you need to cut. Ensure the machine’s cutting bed is large enough to accommodate your largest materials comfortably.
- Precision and Quality: Look for a machine with high precision and excellent cutting quality, especially if your projects require fine details or tight tolerances.
- Features and Options: Evaluate additional features such as automatic loading/unloading systems, dual worktables, rotary axes for pipe cutting, and advanced control systems. These features can enhance productivity and expand the machine’s versatility.
- Brand and Manufacturer: Choose a reputable brand with a proven track record for quality, reliability, and customer support. Research reviews and seek recommendations from industry peers to ensure you’re getting a reliable machine.
- Software and Controls: Ensure the machine’s software is user-friendly and compatible with your design files. Advanced control systems can improve efficiency and ease of operation.
- Maintenance and Support: Consider the availability of ongoing maintenance services, spare parts, and technical support. A strong support network is crucial for minimizing downtime and maximizing machine life.
- Budget: Set a budget that accommodates not only the initial purchase price but also installation, training, and ongoing maintenance costs. Choose a machine that provides the best value within your financial range.
- Future Needs: Anticipate your future production needs and choose a machine that can scale with your business. A machine with extra capacity can prevent the need for an upgrade too soon.
How Are Fiber Laser Cutting Machines Maintained?
- Daily Maintenance
- Clean the Machine: Remove dust and debris from the machine’s surface, cutting area, and surrounding environment to avoid contamination that could affect performance.
- Check the Optics: Inspect and clean the laser lens and mirrors regularly to prevent the buildup of dust or residue, which can degrade cutting quality.
- Lubricate Moving Parts: Apply lubricant to guide rails, screws, and other moving parts to ensure smooth operation and prevent wear.
- Weekly Maintenance
- Inspect and Clean Nozzles: Ensure that cutting nozzles are free from blockages and damage. Clean them regularly for optimal cutting efficiency.
- Check Gas Supply: Verify the levels and flow of cutting gases (e.g., nitrogen, oxygen) and ensure there are no leaks that could affect the cutting process.
- Inspect Cooling System: Ensure that the cooling system is functioning correctly by checking coolant levels and cleaning filters to prevent overheating.
- Monthly Maintenance
- Calibrate the Machine: Perform a full calibration to ensure that the machine delivers precise cuts and operates with maximum accuracy.
- Inspect Electrical Connections: Check all electrical connections for signs of wear, loose wiring, or potential issues, and tighten them as needed.
- Check the Drive System: Inspect gears, and pulleys for wear and replace them if necessary to avoid performance degradation.
- Quarterly Maintenance
- Inspect and Replace Filters: Clean or replace the air filters in both the laser source and cooling system to ensure optimal airflow and prevent dust contamination.
- Check Software and Firmware: Update software and firmware to the latest versions to ensure the machine runs efficiently and has access to the latest features.
- Test Safety Systems: Regularly test safety systems, such as emergency stop buttons and interlocks, to ensure they function correctly in case of an emergency.
- Annual Maintenance
- Professional Servicing: Schedule an annual service with a qualified technician to conduct a comprehensive inspection and maintenance check.
- Alignment Check: Perform a detailed laser beam and optical component alignment to ensure cutting accuracy and avoid any performance issues.
- Review and Replace Worn Parts: Evaluate the condition of critical components and replace any parts that show significant wear or are nearing the end of their lifespan.
- General Best Practices
- Maintain a Clean Environment: Keep the cutting area and surrounding environment clean to minimize dust or debris that could affect the machine’s performance.
- Follow Manufacturer Guidelines: Always refer to the manufacturer’s specific maintenance recommendations for your machine model to avoid any unnecessary issues.
- Train Operators: Ensure all operators are properly trained on both machine operation and basic maintenance tasks to prevent operational errors.
How Accurately Does Fiber Laser Cutting Machines Cut?
- Dimensional Accuracy: Generally within ±0.03 mm to ±0.1 mm, depending on the machine’s configuration and quality.
- Repeatability: Fiber lasers can consistently cut the same shape or pattern with minimal deviation, typically within ±0.02 mm to ±0.05 mm.
- Cutting Edge Quality: Fiber lasers produce smooth, clean edges with minimal burrs, particularly on thin to medium-thickness materials, ensuring high-quality cuts.
- Kerf Width: The kerf (the width of the cut) is usually between 0.1 mm and 0.3 mm, providing the ability to cut intricate designs with fine details.
What Is The Life Expectancy of Fiber Laser Cutting Machines?
- Quality of Components: Machines with high-quality components, such as reliable laser sources, precision optics, and durable mechanical parts, tend to last longer.
- Usage Intensity: High-production environments with continuous operation may lead to more wear and tear, reducing the machine’s lifespan compared to those used less frequently.
- Maintenance: Proper and regular maintenance, including cleaning, lubrication, calibration, and timely replacement of worn parts, is crucial in extending the life of the machine.
- Operating Environment: A clean, controlled environment with stable temperature and humidity levels helps protect the machine from dust, debris, and environmental wear.
- Technological Advancements: While the physical components of the machine can last many years, technological advancements may eventually make older models less efficient or competitive. However, with appropriate upgrades and maintenance, older machines can still be highly functional.
- Manufacturer Support: Ongoing support from the manufacturer, including access to spare parts, software updates, and system upgrades, can help maximize the lifespan of the machine.
What Kind of Cooling System Do Fiber Laser Cutting Machines Use?
- Chiller Unit: The heart of the cooling system is the chiller unit, which circulates chilled water to cool critical components such as the laser source, optics, and, in some cases, the cutting head and power supply. It effectively removes excess heat and maintains a stable operating temperature.
- Water Circulation: A circulation loop is integrated into the system, running through the laser source and other key parts. The water absorbs heat from these components and is then returned to the chiller to be re-cooled and reused.
- Temperature Control: The chiller is equipped with temperature control systems that maintain the water within a specific temperature range. This precision is vital, as temperature fluctuations can negatively affect the performance and lifespan of the laser components.
- Cooling Capacity: The cooling system’s capacity is carefully matched to the power of the laser. Higher-powered lasers require more robust cooling systems to handle the increased heat production.
- Deionized Water: Deionized water is often used to prevent mineral buildup and corrosion, which could degrade the system’s efficiency and damage critical components.
- Coolant Filters: Some cooling systems feature coolant filters that help maintain the purity of the water, removing impurities that could impact cooling efficiency and overall machine performance.
Related Resources
Laser Marking VS Screen Printing
Laser Welding VS MIG Welding
Laser Rust Removal VS Sandblasting Rust Removal
Fiber Laser Cutting VS Plasma Cutting
Contact Us
Contact Information Form: