Introduction
Handheld Laser Welding Machines
-
VIW Laser Welding Machine
Rated 4.75 out of 5$3,800.00 – $8,400.00 Select options This product has multiple variants. The options may be chosen on the product page -
VIW-A Laser Welding Machine
Rated 4.50 out of 5$4,000.00 – $6,000.00 Select options This product has multiple variants. The options may be chosen on the product page -
VIW-P Laser Welding Machine
Rated 5.00 out of 5$3,800.00 – $8,400.00 Select options This product has multiple variants. The options may be chosen on the product page -
VIW-D Laser Welding Machine
Rated 4.75 out of 5$4,600.00 – $9,200.00 Select options This product has multiple variants. The options may be chosen on the product page -
VIW-S Laser Welding Machine
Rated 4.75 out of 5$4,300.00 – $8,900.00 Select options This product has multiple variants. The options may be chosen on the product page -
VIW-T Laser Welding Machine
Rated 4.75 out of 5$4,300.00 – $8,900.00 Select options This product has multiple variants. The options may be chosen on the product page -
VIW-F Laser Welding Machine
Rated 5.00 out of 5$4,800.00 – $9,400.00 Select options This product has multiple variants. The options may be chosen on the product page
Applications
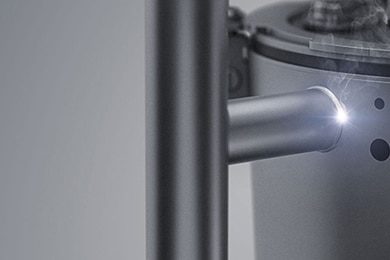
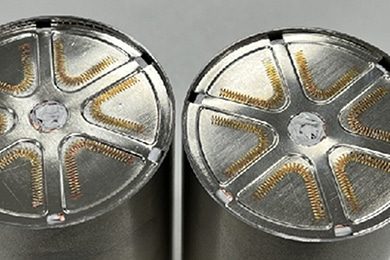
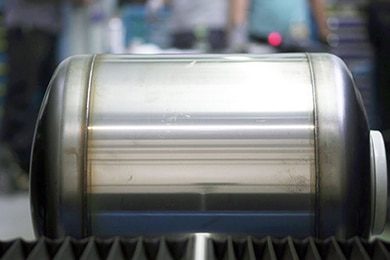
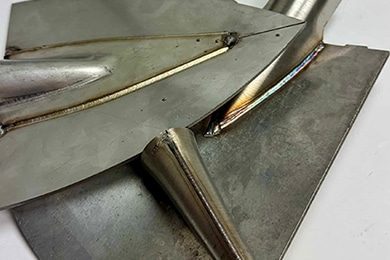
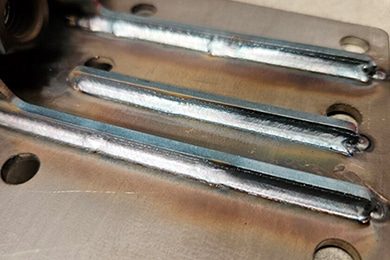
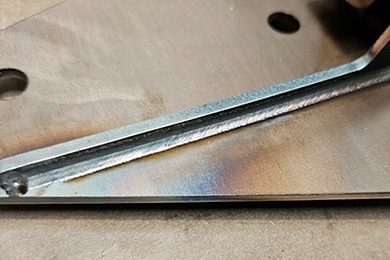
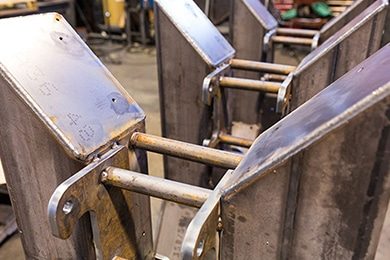
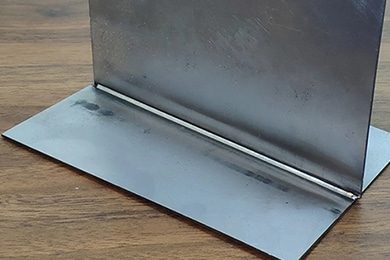
Advantages of Handheld Laser Welding
High Precision and Clean Welds
Handheld laser welding ensures precise, accurate welds with minimal heat distortion, making it ideal for applications that require fine detail, such as electronics and jewelry manufacturing.
Faster Welding Speed
With faster processing times compared to traditional welding, the handheld laser welder increases work efficiency, reducing project timelines and boosting overall productivity without compromising weld quality.
Minimal Material Distortion
Laser welding uses focused energy, which results in less heat transfer to the surrounding material. This minimizes warping, shrinkage, and other thermal distortions, ensuring stronger and more uniform welds.
Portable and Easy to Use
The compact design of the handheld laser welding machine allows for easy handling, enabling operators to reach tight spaces and perform welding tasks in various environments with comfort and flexibility.
Versatility Across Materials
Capable of welding a variety of metals, including stainless steel, aluminum, and copper, the handheld laser welder is a versatile tool suitable for numerous industries, including automotive, electronics, and metalworking.
Low Maintenance Requirements
The advanced technology of the handheld laser welding machine requires minimal maintenance, reducing downtime and operational costs. This makes it a reliable, long-lasting investment for businesses of all sizes.
Comparison with Other Welding Methods
Feature | Laser Welding | MIG Welding | TIG Welding | Arc Welding |
Precision | High precision with minimal heat-affected zones. | Moderate precision, suitable for thicker materials. | Very high precision, ideal for fine work. | Low precision, best for heavy-duty tasks. |
Speed | Fast, with quick weld speeds. | Moderate speed, slower than laser welding. | Slower due to intricate control. | Moderate speed, depending on the material. |
Material Versatility | Can weld a wide range of metals, including thin materials. | Primarily for thicker metals like steel and aluminum. | Works well with thin metals and alloys. | Suitable for heavy-duty metals, less ideal for delicate materials. |
Heat Distortion | Minimal heat distortion, preserving material integrity. | Higher heat input, leading to more distortion. | Low heat input, minimizes material distortion. | High heat input, significant distortion possible. |
Ease of Use | Easy to handle and portable, ideal for detailed and complex tasks. | Requires more experience to control. | Requires skill and patience for precise welds. | Less control, requires significant skill and experience. |
Portability | Highly portable, perfect for on-site and hard-to-reach areas. | Less portable due to equipment size. | Less portable due to equipment and gas requirements. | Requires bulky equipment, not easily portable. |
Weld Quality | Clean, precise, and smooth welds with minimal post-processing. | Good quality, but may require clean-up. | High-quality welds with a smooth finish. | Often requires cleanup and may have spatter. |
Material Thickness | Best for thin to medium thickness materials. | Best for medium to thick materials. | Best for thin materials. | Best for thick materials and heavy-duty jobs. |
Maintenance | Low maintenance with minimal downtime. | Moderate maintenance required. | High maintenance due to delicate equipment. | High maintenance due to wear and tear. |
Cost | Higher upfront cost but lower long-term operational costs. | Lower initial cost but higher consumable costs. | Higher initial cost, but low consumable costs. | Low initial cost, higher operational costs. |
Customer Reviews
Frequently Asked Questions
What Are Handheld Laser Welding Machines?
How Much Do Handheld Laser Welding Machines Cost?
- Entry-Level Models: These machines generally cost between $4,000 and $5,000. They have lower power outputs and fewer advanced features, but they are still suitable for small-scale operations or less demanding welding tasks.
- Mid-Range Models: Priced between $5,000 and $8,000, mid-range models offer higher power, more versatility, and additional features such as adjustable welding modes, improved cooling systems, and better ergonomics. These are ideal for more demanding applications and businesses with moderate workloads.
- High-End Models: High-end machines can cost anywhere from $8,000 to $10,000 or more. These models feature the latest technology, including higher power levels, exceptional precision, faster welding speeds, and the ability to weld a wider variety of materials and thicknesses. They are typically used in industrial settings where performance and reliability are paramount.
How Portable Are Handheld Laser Welding Machines?
- Compact and Lightweight Design: These machines are typically lightweight, ranging from 10 to 30 kilograms (22 to 66 pounds), which allows operators to carry them easily between different work sites or move them around a workshop with minimal effort.
- Ergonomic Handheld Welding Head: The welding head is ergonomically designed to provide a comfortable grip, reducing operator fatigue during extended use. The lightweight and balanced design of the head makes it especially easy to maneuver in tight or hard-to-reach spaces.
- Integrated Power Source: Handheld laser welding machines come equipped with integrated power sources, eliminating the need for external power equipment. Some models even offer battery options, which further enhance portability by allowing use in locations without direct access to power outlets.
- Rugged and Durable Construction: Built to withstand the challenges of transport and on-site use, these machines are constructed with durable materials. This rugged design ensures reliability and performance, even in demanding environments.
- Mobility Features: Many handheld laser welding machines come with additional mobility features such as wheels, handles, or carrying cases. These features make it easier to transport heavier models or move the machine between work areas.
- Versatile Applications: Thanks to their portability, these machines are perfect for on-site repairs, maintenance tasks, and fieldwork, where bringing bulky, stationary equipment would be impractical.
Is Handheld Laser Welding Machine Easy to Operate?
- User-Friendly Interface: Handheld laser welding machines come with intuitive control panels that allow users to adjust settings such as power output, welding speed, and laser intensity. The digital displays and simple controls make it easy to set up and operate the machine.
- Ergonomic Design: The welding head is designed for comfort and ease of use. Its ergonomic design reduces fatigue during prolonged operation and allows the user to maintain control, even in tight or awkward spaces.
- Minimal Setup Requirements: Unlike traditional welding machines that often require complex setups, handheld laser welding machines are typically ready to use with minimal preparation. Basic power connections and simple adjustments are all that’s needed to start welding quickly.
- Automatic Features: Many handheld laser welding machines come equipped with automatic features, such as auto-focus, which adjusts the laser beam for optimal performance based on material and thickness. This reduces the need for manual adjustments and makes the process much easier for the operator.
- Safety Features: These machines are equipped with built-in safety features, including protective shields, interlocks, and emergency stop buttons. These mechanisms not only protect the user but also simplify operations by preventing common mistakes.
- Training and Support: Manufacturers often offer training materials, user guides, and customer support to help new users quickly learn how to operate the machine. This support reduces the learning curve and boosts confidence.
- Less Skill-Dependent: While traditional welding requires significant skill to achieve consistent results, handheld laser welding machines are more forgiving. Even less experienced users can produce high-quality welds with minimal effort.
What Are the Disadvantages of Handheld Laser Welding Machines?
- High Initial Cost: Handheld laser welding machines are typically more expensive than traditional welding equipment. The initial cost, especially for high-powered or advanced models, can be a significant barrier for small businesses or individual users with limited budgets.
- Learning Curve: Although designed for ease of use, there can still be a learning curve, especially for those new to laser welding technology. Operators may need time to familiarize themselves with the machine’s features, capabilities, and safety protocols.
- Limited Material Compatibility: Handheld laser welding machines are versatile but may not be suitable for all materials. Certain plastics, reflective metals like copper or aluminum, and some alloys may require special settings or might not be compatible with standard handheld lasers.
- Power Requirements: These machines require a stable, high-power electrical supply. In some work environments, this may not be readily available, requiring additional infrastructure like dedicated power lines or voltage stabilizers.
- Maintenance and Consumables: Regular maintenance is essential for optimal performance, including cleaning optical components, replacing protective lenses, and managing cooling systems. Consumables, such as lenses and nozzles, can also add to operational costs over time.
- Safety Concerns: While they come with safety features, handheld laser welding machines can still pose risks if not used properly. The high-intensity laser can cause severe injuries, such as eye damage and burns if safety protocols are ignored. Proper training and protective gear are necessary.
- Environmental Limitations: Environmental factors such as temperature, humidity, and dust can impact the performance of handheld laser welders. In uncontrolled environments, these factors may lead to inconsistent weld quality or even damage to the machine.
- Portability Constraints: Although designed for portability, some models, especially those with integrated cooling systems or additional components like gas supplies, can still be somewhat bulky. This can make transportation and setup in remote or confined spaces more difficult.
- Limited Depth of Weld: Handheld laser welding machines are ideal for thin to medium materials, but they may not be suitable for very thick materials. Their weld depth is limited compared to larger, stationary laser systems, making them less effective for deep weld applications.
- Dependence on Clean Surfaces: Laser welding requires clean, well-prepared surfaces. Contaminants like oil, rust, or dirt can compromise weld quality, leading to defects or weak joints. Additional preparation time may be necessary to ensure proper results.
How Fast Are Handheld Laser Welding Machines?
- Welding Speed Range: Handheld laser welding machines generally operate at speeds between 10 mm/s to 50 mm/s or higher, depending on the material and settings. For thin materials like stainless steel, welding can be done quickly, while thicker materials may require slower speeds for optimal fusion.
- Comparison with Traditional Methods: Laser welding is faster than traditional methods like TIG or MIG welding. Laser welding machines achieve deep penetration and high-quality welds in a single pass, whereas traditional techniques may require multiple passes and additional post-processing.
- Material and Thickness Influence: The welding speed varies with material type and thickness. Thin metals, such as sheet steel, can be welded at speeds exceeding 30-40 mm/s. For thicker materials, welding speeds may slow to ensure adequate penetration and weld strength.
- High Precision with Speed: Even at high speeds, handheld laser welding machines maintain excellent precision. This results in clean, accurate welds that minimize the need for additional finishing work, enhancing overall productivity.
- Batch Processing Efficiency: In batch or repetitive tasks, the speed of handheld laser welding machines can drastically reduce production time. Operators can complete more welds in less time, boosting efficiency.
- Adjustable Speed Settings: Many handheld laser welding machines come with adjustable speed settings, enabling operators to fine-tune the welding speed for specific jobs. This flexibility allows users to optimize both speed and quality across various applications.
- Impact of Power Output: Higher-powered machines, such as those with 1500W or more, can achieve faster welding speeds compared to lower-powered models. This is particularly beneficial when working with thicker or more challenging materials.
What Is the Service Life of Handheld Laser Welding Machines?
How to Maintain Handheld Laser Welding Machines?
- Regular Cleaning
- Laser Lens: Regularly clean the laser lens to remove dust, debris, and residue that can affect the laser’s performance. Use appropriate cleaning solutions and lint-free wipes.
- Welding Head: Keep the welding head free from dirt and metal particles. Periodic cleaning ensures consistent weld quality.
- Cooling System Maintenance
- Check Coolant Levels: For water-cooled systems, regularly check and refill the coolant to the recommended level. Make sure the coolant is clean and free from contaminants.
- Inspect Cooling System: Periodically inspect the cooling system for leaks or blockages to prevent overheating and maintain optimal cooling efficiency.
- Protective Lens Replacement
- Replace the protective lens in the laser head when it becomes scratched or coated with welding spatter. A worn-out lens can degrade the laser beam quality and affect weld precision.
- Regular Inspections
- Cables and Connections: Inspect all cables and connections for signs of wear, damage, or loose connections. Replace faulty components to avoid electrical issues.
- Moving Parts: Ensure moving parts, like the focus adjustment mechanism, are operating smoothly. Lubricate and replace parts as needed.
- Software Updates
- Keep the machine’s software and firmware up to date to access the latest features, improvements, and bug fixes. Regular updates enhance performance and can introduce new functionalities.
- Environmental Control
- Operating Environment: Store and operate the machine in a clean, dry, and temperature-controlled environment. Extreme temperatures, humidity, or dust can negatively impact performance.
- Ventilation: Ensure proper ventilation to prevent overheating, especially during prolonged use.
- Scheduled Maintenance
- Follow the manufacturer’s recommended maintenance schedule for periodic inspections and professional servicing. This helps identify potential issues early and keeps the machine in top condition.
- Proper Storage
- When not in use, store the machine in a protective case or cover to shield it from dust, moisture, and physical damage.
- Operator Training
- Ensure that all operators are thoroughly trained in proper usage and maintenance procedures. Incorrect handling or misuse can lead to premature wear.
Related Resources
Laser Marking VS Screen Printing
Laser Welding VS MIG Welding
Laser Rust Removal VS Sandblasting Rust Removal
Fiber Laser Cutting VS Plasma Cutting
Contact Us
Contact Information Form: