Introduction
Laser Welding Machines
-
VIW Laser Welding Machine
Rated 4.75 out of 5$3,800.00 – $8,400.00 Select options This product has multiple variants. The options may be chosen on the product page -
VIW-A Laser Welding Machine
Rated 4.50 out of 5$4,000.00 – $6,000.00 Select options This product has multiple variants. The options may be chosen on the product page -
VIW-P Laser Welding Machine
Rated 5.00 out of 5$3,800.00 – $8,400.00 Select options This product has multiple variants. The options may be chosen on the product page -
VIW-D Laser Welding Machine
Rated 4.75 out of 5$4,600.00 – $9,200.00 Select options This product has multiple variants. The options may be chosen on the product page -
VIW-S Laser Welding Machine
Rated 4.75 out of 5$4,300.00 – $8,900.00 Select options This product has multiple variants. The options may be chosen on the product page -
VIW-T Laser Welding Machine
Rated 4.75 out of 5$4,300.00 – $8,900.00 Select options This product has multiple variants. The options may be chosen on the product page -
VIW-F Laser Welding Machine
Rated 5.00 out of 5$4,800.00 – $9,400.00 Select options This product has multiple variants. The options may be chosen on the product page -
VIW-R Laser Welding Machine
Rated 4.50 out of 5$18,800.00 – $23,400.00 Select options This product has multiple variants. The options may be chosen on the product page
Applications
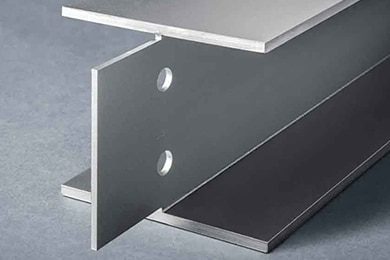
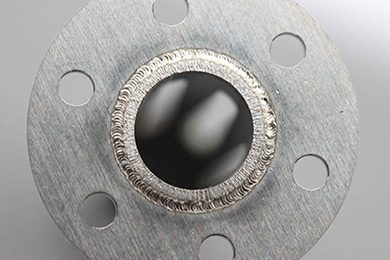
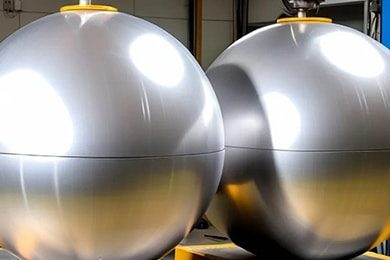
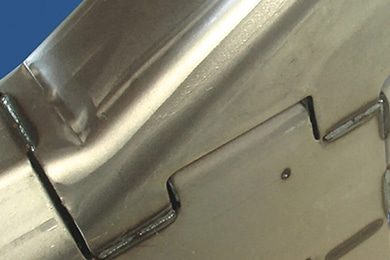
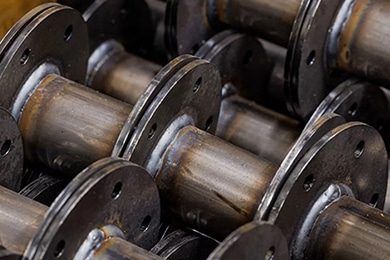
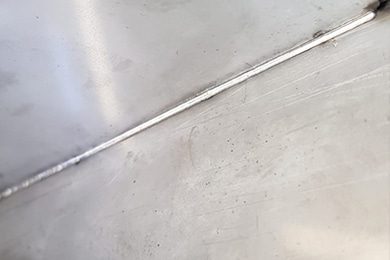
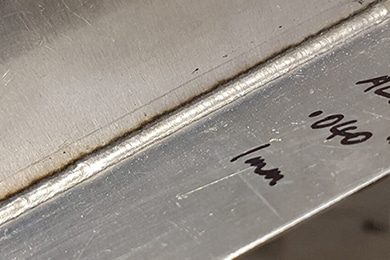
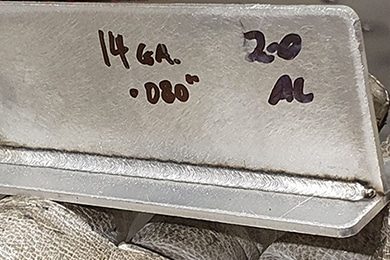
Advantages of Laser Welding
High Precision and Accuracy
Laser welding offers exceptional control, allowing for precise welds in intricate and delicate components. This precision ensures minimal distortion and optimal results, even in complex or small-scale applications.
Minimal Heat Affected Zone
With laser welding, the heat input is focused and localized, resulting in a narrow heat-affected zone. This minimizes thermal distortion, reducing the need for extensive post-weld processing.
Fast Welding Speed
Laser welding provides high-speed processing, significantly reducing production times. Its ability to quickly and efficiently complete welds boosts overall productivity in high-demand manufacturing environments.
Reduced Material Waste
Laser welding’s focused beam minimizes excess material usage, ensuring more efficient use of resources. The process helps reduce waste, contributing to cost savings and more sustainable manufacturing practices.
Versatility with Different Materials
Laser welding can effectively join a wide range of materials, including metals like steel, aluminum, and titanium. Its adaptability makes it suitable for various industries, from automotive to electronics.
High-Quality Welds with Minimal Filler
Laser welding produces strong, clean welds with minimal need for filler materials, ensuring high-quality bonds with smooth, uniform surfaces. This results in superior weld integrity and durability.
Comparison with Other Welding Methods
Feature | Laser Welding | TIG Welding | MIG Welding | Arc Welding |
Welding Speed | Very fast, high-speed welding suitable for mass production | Slow compared to laser, suitable for precision work | Faster than TIG, good for thicker materials | Slow, best for thick, heavy materials |
Precision | High precision, ideal for delicate and intricate components | High precision, suitable for thin metals | Moderate precision, suitable for thicker materials | Lower precision, suited for large parts |
Heat Affected Zone (HAZ) | Very narrow, minimal distortion | Larger HAZ, more distortion due to higher heat input | Moderate HAZ, but more controlled than arc welding | Large HAZ, significant distortion |
Weld Quality | High-quality, clean welds with minimal post-weld processing | High-quality welds, may require clean-up | Decent quality, can have spatter and require clean-up | Lower quality, often requires more post-weld processing |
Material Compatibility | Works well on a variety of metals, including thin and delicate materials like aluminum, titanium | Best for thin materials, like stainless steel | Works on a wide range of materials, including thicker metals | Best for thick materials, like steel and iron |
Automation Capability | Highly automated with advanced control systems, ideal for mass production | Requires more manual intervention | Semi-automated, requires some skill | Mostly manual, limited automation |
Post-Weld Processing | Minimal to no post-weld processing needed | Often requires cleaning or grinding | Can have spatter, requires cleaning | Significant clean-up required |
Cost Efficiency | High initial cost, but low operational cost over time | Moderate cost, higher consumables cost | Moderate cost, consumables needed frequently | Low initial cost, but high consumable costs |
Ease of Use | Requires skilled operators, but highly automated for ease | Requires skilled operators and careful control | Easier for less skilled workers, but still requires practice | Requires significant skill for good results |
Application Range | Ideal for delicate, complex parts across multiple industries (e.g., aerospace, electronics) | Ideal for thin, high-precision welds, mostly in industries like aerospace and medical | Best for thicker materials in industries like automotive and construction | Suitable for large-scale and heavy-duty applications |
Customer Reviews
Frequently Asked Questions
How Much Do Laser Welding Machines Cost?
- Handheld Laser Welding Machines: These versatile and user-friendly machines typically range from $5,000 to $10,000, depending on power levels and features such as cooling systems or automatic wire feeders.
- Automatic Laser Welding Machines: Designed for high-volume production and automation, these machines are more advanced and expensive. Prices usually range from $50,000 to $200,000 or more, based on the complexity, power output, and customization options.
- Portable and Compact Laser Welding Machines: Ideal for smaller-scale or mobile applications, these machines are more affordable, typically costing between $4,000 and $9,000.
Why Are Laser Welding Machines Expensive?
- Advanced Technology
- Laser Source: The heart of a laser welding machine is the laser source, typically a high-quality fiber laser. Manufacturing these lasers is expensive due to the precision and materials required.
- Precision and Control: Sophisticated control systems are needed to manage the laser beam’s power, speed, and focus. This ensures accuracy and repeatability, which is crucial for high-precision applications like aerospace and medical devices.
- High-Quality Components
- Optics and Delivery Systems: The optics that focus and direct the laser are made from specialized materials. These components must withstand high temperatures and maintain precision over time, adding to the overall cost.
- Cooling Systems: High-power laser welding machines often include advanced cooling systems to prevent overheating and extend the machine’s lifespan, which increases the price.
- Durability and Longevity
- Industrial-Grade Build: These machines are built for industrial environments, ensuring durability, reliability, and the ability to operate continuously. This robust construction contributes to the higher cost.
- Long Lifespan: Designed for long-term use with minimal maintenance, laser welding machines justify their initial cost through longevity and reduced maintenance needs.
- Automation and Integration
- Automation Capabilities: Many machines come with advanced automation features, including robotic arms and CNC controls, driving up costs due to their complexity and integration into production lines.
- Customization and Versatility: Machines that can be customized for specific applications or materials increase in value but also in price.
- Research and Development
- Innovation: Significant R&D investments are required to advance laser welding technology. Manufacturers constantly innovate to improve efficiency, precision, and versatility, and these costs are reflected in the price of the machine.
- Support and Training
- Technical Support: High-end machines often come with comprehensive support services, including installation, maintenance, and troubleshooting, which are factored into the price.
- User Training: Due to the complexity of laser welding machines, proper training is necessary for effective operation, and training programs are often included as part of the package.
What Are the Disadvantages of Laser Welding Machines?
- High Initial Cost: Laser welding machines are expensive to purchase, with high upfront costs for the equipment, installation, and necessary infrastructure, such as cooling systems and safety enclosures. This can be a significant financial burden, particularly for small businesses.
- Complex Operation and Maintenance: Operating a laser welding machine requires specialized knowledge and training. These machines are complex, with multiple parameters to control for optimal performance. Maintenance can also be intricate and costly, often requiring skilled technicians.
- Sensitivity to Material Properties: Laser welding is highly sensitive to the material being welded. Variations in properties like reflectivity or thermal conductivity can affect the weld’s quality. For example, reflective materials like aluminum can reduce efficiency by reflecting the laser energy.
- Limited Thickness Capability: While ideal for thin materials, laser welding may not be the best choice for welding very thick metals. Other methods like arc welding or electron beam welding may provide better penetration and stronger welds for thicker materials.
- Heat Affected Zone (HAZ) Issues: Although laser welding generally produces a smaller Heat Affected Zone (HAZ) than other methods, rapid heating, and cooling can cause cracking or changes in material properties, especially with sensitive or brittle materials.
- Safety Concerns: The use of high-powered lasers in welding poses significant safety risks, including eye injuries, skin burns, or fires. Proper safety protocols, such as protective eyewear, enclosures, and comprehensive training, are essential but add to the operational complexity and cost.
- High Energy Consumption: Laser welding machines, particularly high-power models, consume a substantial amount of energy. This can lead to increased operational costs, particularly in high-volume industrial environments.
- Limited Joint Configuration: Laser welding is most effective for certain joint configurations like butt or lap joints. It may not be suitable for more complex or irregular geometries, limiting its versatility for some applications.
- Requirement for Precision Fixturing: For optimal weld quality, workpieces must be precisely positioned and held in place. This often requires specialized fixturing, increasing setup time and costs, especially in high-volume production environments.
- Material Compatibility Limitations: While laser welding is versatile, it may not be suitable for all materials or material combinations. Welding dissimilar metals with significantly different thermal properties can be difficult and may require specialized control.
How Thick Can Laser Welding Machines Weld?
- Stainless Steel
- Weldable Thickness: Up to 5-6 mm in a single pass
- Notes: Fiber lasers are ideal for welding stainless steel due to their excellent absorption properties. For thicker sections, multiple passes or speed/power adjustments may be required.
- Aluminum
- Weldable Thickness: Up to 4-5 mm in a single pass
- Notes: Aluminum’s high thermal conductivity and reflectivity make it challenging, but high-power fiber lasers can achieve strong welds. Pre-heating or pulsed laser methods help with thicker sections.
- Carbon Steel
- Weldable Thickness: Up to 5-6 mm in a single pass
- Notes: Carbon steel is easier to weld with fiber lasers, thanks to low reflectivity. Thicker materials may need multiple passes or power adjustments.
- Copper
- Weldable Thickness: Up to 3-4 mm in a single pass
- Notes: Copper is highly reflective and has high thermal conductivity, requiring techniques like beam shaping or shorter wavelengths to achieve quality welds.
- Brass
- Weldable Thickness: Up to 2-4 mm in a single pass
- Notes: Like copper, brass is also reflective and conductive, requiring precise control of laser parameters for optimal welding results.
- Titanium
- Weldable Thickness: Up to 4-5 mm in a single pass
- Notes: Titanium is well-suited for fiber laser welding due to its high absorptivity. It’s often used in aerospace and medical applications where precision is essential.
- Nickel Alloys
- Weldable Thickness: Up to 4-5 mm in a single pass
- Notes: Nickel alloys, used in high-performance applications, weld effectively with fiber lasers, though cooling and power settings must be carefully managed to avoid cracking.
- Galvanized Steel
- Weldable Thickness: Up to 2-3 mm in a single pass
- Notes: Galvanized steel can be welded with fiber lasers, but the zinc coating often leads to porosity. Careful control of laser parameters and post-weld processing are necessary.
- Inconel
- Weldable Thickness: Up to 4-5 mm in a single pass
- Notes: Inconel, a high-performance alloy, can be effectively welded with fiber lasers, especially in extreme environments, though it requires precise control of heat and power.
What Is The Service Life of Laser Welding Machines?
- Laser Source
- Fiber Lasers: The fiber laser source typically has a service life of 20,000 to 30,000 hours of operation. Fiber lasers are more durable and reliable compared to other laser types, making them suitable for high-performance industrial applications. Many machines come with warranties and service contracts to ensure their longevity and provide a safeguard against premature failure.
- Machine Components
- Optics: Optical components, including lenses and mirrors, generally need replacement or servicing every 1 to 2 years depending on usage. With proper handling and regular cleaning, the lifespan of these optical components can be extended.
- Cooling Systems: Cooling systems, typically using water to manage heat, have a service life of around 5 to 10 years. Regular maintenance, such as replacing filters and checking cooling components, is essential to ensure efficient machine operation and prevent overheating.
- Mechanical Parts
- Motion Systems: Mechanical components such as servo motors, linear guides, and other motion systems are designed for long-term use. With proper maintenance, these parts can last anywhere from 5 to 10 years. Regular lubrication and inspection of the motion system are crucial to extending its lifespan.
- Worktables and Fixtures: Worktables, fixtures, and other support components typically last between 5 to 10 years depending on the intensity of usage and maintenance practices. These parts are subject to wear and tear, especially in high-volume production environments, but proper care can prolong their service life.
- Overall Machine Service Life
- High-Quality Laser Welding Machines: With proper care and maintenance, high-quality laser welding machines can last anywhere from 10 to 15 years. Factors such as operational conditions, the frequency of use, and adherence to recommended maintenance schedules significantly impact the machine’s overall lifespan.
- Maintenance and Upgrades: Regular servicing, timely repairs, and adherence to maintenance guidelines can help extend the machine’s operational life. However, technological advancements may render older models less competitive, even if they continue functioning.
Does Laser Welding Machines Require Gas?
- Shielding Gas: Shielding gases are used to protect the weld area from oxidation, contamination, and atmospheric impurities. They create an inert atmosphere around the weld pool, ensuring a clean weld and preventing defects such as porosity.
- Argon: Frequently used for its cost-effectiveness and availability. Argon is a noble gas that does not react with the material being welded, making it ideal for shielding.
- Helium: Provides better heat transfer and deeper penetration compared to argon. It is used in applications where higher heat and better weld penetration are needed, such as welding thick or high-melting-point materials.
- Assist Gas: Assist gases are used to help blow away molten material, slag, and fumes from the weld zone, thereby improving the quality of the weld and enhancing the overall efficiency of the welding process. They can also increase heat or modify the characteristics of the welding process.
- Oxygen: Oxygen is commonly used in laser cutting and welding, particularly with materials like steel. It helps to increase the heat in the weld zone and can promote exothermic reactions that improve the welding process. However, it can also cause oxidation if not controlled properly.
- Nitrogen: Nitrogen is used in laser welding to prevent oxidation and produce cleaner, more aesthetically pleasing welds, especially when working with stainless steel. Nitrogen can also be used to enhance cutting performance in certain materials.
- Material-Specific Gas Requirements
- Stainless Steel: Shielding gases like argon are commonly used for welding stainless steel to prevent oxidation and ensure a clean, high-quality weld.
- Aluminum: Aluminum’s high thermal conductivity and sensitivity to oxidation require gases that enhance heat transfer. Helium or a mixture of argon and helium is often used to achieve better weld quality and improved penetration.
- Copper: Copper is highly reflective and has high thermal conductivity, making it more challenging to weld. Special gas mixtures, such as a blend of argon and helium, are often used to handle copper’s challenging properties and improve weld penetration.
- Cooling Gas (Less Common)
- Purpose: Some laser welding applications may use gases for cooling purposes to manage the thermal load, especially when using high-power lasers.
- Common Gases: While not a primary focus in most laser welding applications, argon or nitrogen may be used for cooling, particularly in high-intensity laser welding processes.
Does Laser Welding Machines Use Welding Wire?
- Autogenous Laser Welding (No Welding Wire): In this process, the laser beam directly melts the base metals at the joint, causing them to fuse. There is no filler material (welding wire) added to the weld pool.
- Applications: Ideal for thin materials or precision welding where no additional material is required. It is often used in applications that demand minimal heat input and where the joint geometry doesn’t require extra material to fill gaps.
- Advantages: Simplifies the process, reduces material costs, and provides cleaner welds with high precision.
- Filler Wire Laser Welding (With Welding Wire): This technique involves feeding filler wire into the weld area. The laser beam melts both the base metal and the filler wire to form the weld.
- Applications: Used for welding thicker materials, filling gaps, or when a specific weld profile is required. This process is particularly beneficial in situations where the weld joint is not perfectly aligned, and the extra material helps to ensure a more robust joint.
- Advantages: Provides additional strength to the weld, helps with joining materials of varying thicknesses, and can be used for repairs or when welding gaps.
What Is The Difference Between MIG And Laser Welding Machines?
- Welding Process
- MIG Welding: MIG welding, also known as Gas Metal Arc Welding (GMAW), uses an electric arc to melt and join metal pieces. A continuous solid wire electrode is fed through a welding gun into the weld pool, where it melts and fuses with the base material. An inert or semi-inert shielding gas, such as argon or CO2, is used to protect the weld pool from atmospheric contamination.
- Laser Welding: In laser welding, a high-powered laser beam is focused to melt and fuse materials with precision. The concentrated heat from the laser allows for deep penetration and fine control. Shielding gases like argon, helium, or nitrogen are commonly used to protect the weld zone from oxidation and contamination.
- Equipment
- MIG Welding: MIG welding requires a welding gun, a wire feed system, a power supply, and a shielding gas setup. The equipment is generally bulkier, as it includes components such as a gas cylinder and a wire feeder.
- Laser Welding: Laser welding setups consist of a laser source, focusing optics to direct the beam, and a shielding gas system. The equipment is typically more compact and precise but requires specialized and costly components.
- Precision and Control
- MIG Welding: MIG welding is less precise compared to laser welding. It is more suitable for thicker materials where fine control isn’t crucial. MIG welding is easier to learn and operate, making it versatile for various applications.
- Laser Welding: Laser welding provides exceptional precision and control, making it ideal for detailed, intricate tasks. It can achieve deep penetration with minimal heat-affected zones, allowing for delicate, high-precision work. However, it requires more specialized skills and training to operate effectively.
- Speed and Efficiency
- MIG Welding: MIG welding is generally slower than laser welding and works well for applications where speed isn’t the primary concern. While it is effective for a wide range of metals and thicknesses, it is less efficient in terms of material usage and precision.
- Laser Welding: Laser welding is faster due to the concentrated energy of the laser beam. It is ideal for high-volume production and automated processes, offering superior efficiency with minimal material distortion and waste.
- Applications
- MIG Welding: Commonly used in industries such as automotive, construction, and general manufacturing. It is ideal for welding thicker metals like steel and aluminum and is versatile enough for a wide range of materials and thicknesses.
- Laser Welding: Frequently used in industries like aerospace, medical device manufacturing, electronics, and precision engineering. It excels in welding thin materials and applications that require high precision. Laser welding also offers superior weld quality, minimal distortion, and the ability to weld dissimilar materials.
- Costs
- MIG Welding: MIG welding has a lower initial equipment cost and setup. However, it incurs higher consumable costs due to the continuous use of wire and shielding gases.
- Laser Welding: While laser welding requires a higher initial investment due to the advanced technology involved, its efficiency leads to cost savings in the long term, especially for high-volume production. Additionally, it has lower consumable costs, as the equipment is more efficient and uses less material.
Related Resources
Laser Marking VS Screen Printing
Laser Welding VS MIG Welding
Laser Rust Removal VS Sandblasting Rust Removal
Fiber Laser Cutting VS Plasma Cutting
Contact Us
Contact Information Form: