Introduction
Tube Laser Cutting Machines
-
VIT Laser Cutting Machine
Rated 4.75 out of 5$24,300.00 – $167,500.00 Select options This product has multiple variants. The options may be chosen on the product page -
VIT-A Laser Cutting Machine
Rated 5.00 out of 5$79,300.00 – $222,500.00 Select options This product has multiple variants. The options may be chosen on the product page
Applications
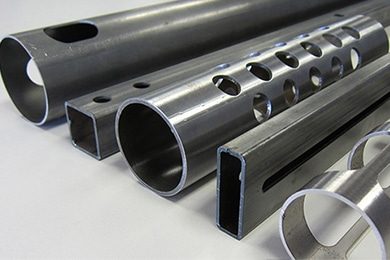
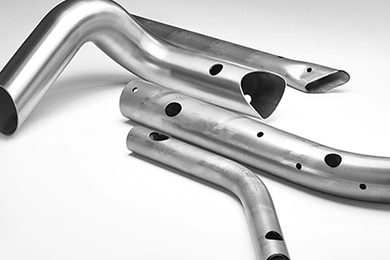
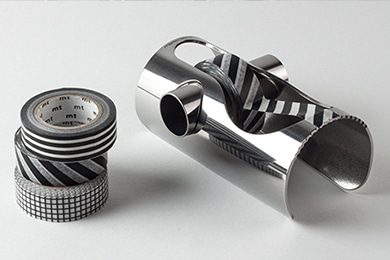
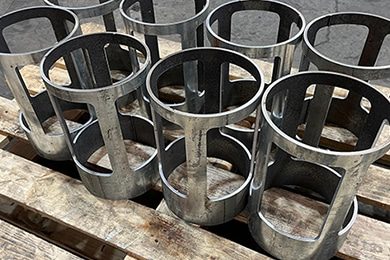
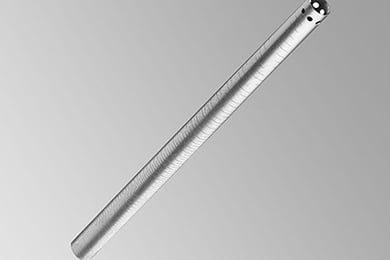
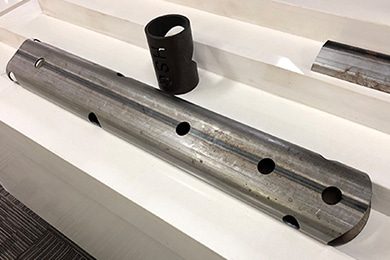
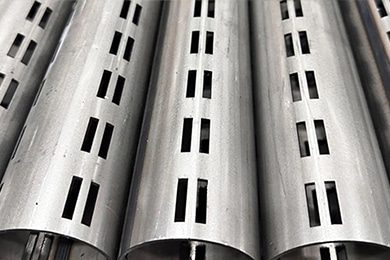
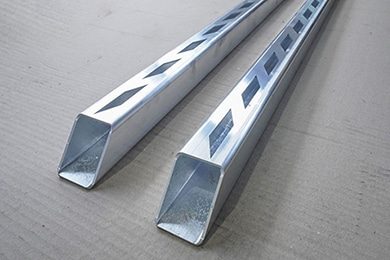
Advantages of Tube Laser Cutting
High Precision
Tube laser cutting provides exceptional accuracy, ensuring clean, burr-free cuts with tight tolerances. This precision eliminates the need for post-processing, improving the overall quality of your components.
Versatility in Cutting Shapes
From round to square and rectangular tubes, as well as custom profiles, tube laser cutting machines can handle a wide variety of shapes and sizes, making them suitable for diverse fabrication projects.
Reduced Material Waste
Laser cutting minimizes material wastage by optimizing cut patterns. This cost-effective process maximizes material usage, helping businesses reduce scrap and lower production costs.
Faster Production Times
With automated features and high-speed cutting, tube laser cutting reduces production cycles, allowing for quicker turnaround times. This boosts efficiency and enables higher throughput in manufacturing environments.
Ability to Cut Multiple Materials
Tube laser cutting machines can process a range of materials, including stainless steel, carbon steel, and aluminum, offering flexibility for different applications and industries.
Enhanced Safety and Automation
Automated operations and minimal manual intervention improve safety and reduce the risk of human error. With built-in safeguards, tube laser cutting systems provide a more secure and efficient working environment.
Comparison with Other Cutting Methods
Feature | Laser Cutting | Plasma Cutting | Waterjet Cutting | Flame Cutting |
Precision | High precision, clean, burr-free cuts | Moderate precision can leave rough edges | High precision, ideal for complex shapes | Lower precision, rough edges |
Cutting Speed | Very fast, ideal for high-volume production | Fast, but slower than laser cutting | Slower than laser cutting due to water pressure | Slower compared to other methods |
Material Versatility | Works on a wide range of metals like steel, aluminum, and stainless steel | Primarily used for conductive metals like steel | Works on almost any material, including metals and stone | Primarily used for thicker metals like steel |
Thickness Limit | Can cut thin to thick tubes with high precision | Best for thicker materials | Can cut very thick materials, but slower than plasma | Best for thick materials (up to several inches thick) |
Heat Affected Zone (HAZ) | Minimal HAZ, preserving material properties | Larger HAZ may affect material properties | Very minimal HAZ due to cold cutting process | Large HAZ, can affect material strength and finish |
Material Waste | Low material waste due to precise cutting patterns | Higher material waste due to rougher cuts | Minimal material waste, but can be slower and costlier | Higher waste due to rough edges and less efficient cutting |
Surface Finish | Smooth, clean surface with little to no post-processing | Rough finish, often requiring additional finishing | Smooth surface, minimal post-processing required | Rough surface, often requiring grinding or finishing |
Cost Efficiency | High initial cost, but cost-effective in high-volume production | Lower initial cost, but higher operational costs for thick materials | Moderate initial cost, ideal for a variety of materials | Low initial cost but high operational costs for thick materials |
Automation | Fully automated, reducing labor and increasing throughput | Semi-automated, may require more manual adjustments | Highly automated, but slower cutting speeds | Often manual, with limited automation options |
Environmental Impact | Minimal environmental impact due to efficient cutting | Generates fumes, requiring ventilation | No heat or fumes, more eco-friendly | Produces smoke and requires ventilation |
Customer Reviews
Frequently Asked Questions
What Are Tube Laser Cutting Machines?
How Do Tube Laser Cutting Machines Work?
- Laser Source: The process begins with the laser source, typically a fiber laser, which generates a concentrated beam of light. This beam contains immense energy, which is then focused on the material to initiate the cutting process.
- Beam Delivery: The laser beam travels through a series of mirrors and lenses within the cutting head, ensuring that it is accurately directed and focused on the exact cutting area of the tube.
- Cutting Head: The cutting head houses the focusing lens and optical components that direct the laser beam onto the material. The head moves along multiple axes to follow the programmed cutting path, ensuring precision and adaptability.
- Rotary Axis: A key feature of tube laser cutting machines is the rotary axis, which allows the tube to rotate during the cutting process. This rotation enables the machine to cut all around the tube, making it possible to create complex features and shapes on its circumference.
- Control System: Tube laser cutting machines are controlled by sophisticated software that manages the entire cutting process. The software regulates cutting paths, speed, and laser power, allowing for intricate designs and accurate execution of complex cuts.
- Material Handling: Many machines incorporate automated systems to load and unload tubes, ensuring quick and precise positioning for each cut. This automation streamlines the process, reducing manual labor and increasing efficiency.
- Cutting Process: As the focused laser beam heats the material, it melts or vaporizes the metal, creating a clean and precise cut. The machine’s high-speed cutting capabilities and minimal heat-affected zone (HAZ) ensure top-quality results with minimal waste.
- Post-Cutting Operations: After the cutting is complete, the finished parts are inspected for accuracy. Depending on the application, additional post-processing, such as deburring or surface finishing, may be carried out to meet quality standards.
What Is The Price Of Tube Laser Cutting Machines?
- Entry-Level Models: Prices typically range from $25,000 to $45,000. These machines usually have lower power levels, smaller cutting capacities, and fewer advanced features, making them suitable for simpler applications.
- Mid-Range Models: These machines offer higher power, larger cutting capacities, and more features, with prices typically ranging from $50,000 to $100,000. They are suitable for businesses looking to scale their operations.
- High-End or Industrial-Grade Models: The most advanced tube laser cutting machines, which include the highest power levels, large cutting capacities, automation features, and customization options, can cost anywhere from $150,000 to $500,000.
What Is The Maximum Tube Diameter And Length Tube Laser Cutting Machines Can Cut?
- Maximum Tube Diameter: With the ability to cut tubes up to 500mm in diameter, these machines can process large-diameter tubes used in industries such as construction, infrastructure, and manufacturing. This capability allows for the precise cutting of structural components, support beams, and large-scale parts.
- Maximum Tube Length: The ability to cut tubes up to 9 meters long greatly expands the machine’s versatility, making it suitable for applications in industries like aerospace, transportation, and energy. It is ideal for cutting long tubes for pipelines, exhaust systems, structural frameworks, and architectural elements.
How To Maintain Tube Laser Cutting Machines?
- Daily Maintenance
- Clean the Cutting Head: Regularly clean the cutting head, lenses, and mirrors to remove dust and debris. This ensures the laser beam stays focused and effective.
- Check the Optics: Inspect lenses and mirrors for damage or contamination. Clean them with appropriate solutions and soft, lint-free cloths to maintain cutting precision.
- Inspect the Nozzle: Ensure the cutting nozzle is clear of blockages. Clean or replace it if needed to maintain consistent cutting quality.
- Check Gas Pressure: Verify that the assist gas (typically nitrogen or oxygen) pressure is at the correct level for the materials being cut.
- Weekly Maintenance
- Check Alignment: Ensure that the laser beam is properly aligned with the cutting head. Misalignment can degrade cut quality and increase machine wear.
- Inspect the Rotary Axis: For machines with a rotary axis, ensure smooth operation and check for excessive play or resistance.
- Lubricate Moving Parts: Apply lubricant to moving parts like guide rails and bearings to reduce friction and prevent wear.
- Clean the Work Area: Remove metal shavings, dust, or debris from the work area and machine enclosure to prevent contamination of sensitive components.
- Monthly Maintenance
- Check the Cooling System: Inspect the cooling system (including the water chiller) for leaks or blockages. Ensure the coolant is at the correct level and replace it if contaminated.
- Inspect Electrical Connections: Examine all electrical connections for wear, corrosion, or loose components. Secure any loose wires and replace damaged parts.
- Test Safety Systems: Verify that all safety features (e.g., interlocks, and emergency stops) are functioning correctly to ensure operator safety.
- Clean the Exhaust System: Ensure the exhaust system works properly. Clean or replace filters as needed to maintain airflow and remove fumes.
- Annual Maintenance
- Full System Calibration: Perform a full calibration of the laser cutting system to ensure it operates to manufacturer specifications. This may involve realigning the laser and adjusting optics.
- Inspect the Laser Source: Check the condition of the laser source, including the resonator and power supply. Follow manufacturer guidelines for specific maintenance tasks.
- Professional Servicing: Consider scheduling professional servicing for in-depth inspections and maintenance that exceed regular upkeep.
- General Tips
- Follow Manufacturer’s Guidelines: Always adhere to the manufacturer’s maintenance schedule and recommendations for your specific model.
- Keep a Maintenance Log: Track all maintenance activities, including inspections, cleanings, and part replacements, to identify potential issues early.
- Operator Training: Ensure operators are well-trained in both operating the machine and performing routine maintenance tasks.
How Does Tube Laser Cutting Machines Reduce Material Waste?
- Precision Cutting
- Minimal Kerf Width: The laser beam is extremely narrow, producing a small kerf that minimizes material loss during cutting.
- Accurate Cutting: High precision ensures cuts are made exactly where needed, reducing the risk of errors and material waste.
- Optimized Nesting
- Advanced Software: Sophisticated software optimizes the cutting layout, arranging multiple parts efficiently to minimize gaps and reduce offcuts.
- Custom Shapes and Geometries: The machine’s ability to cut complex shapes allows for better material utilization and fewer wasteful offcuts.
- Versatility in Tube Shapes and Sizes
- Handling Various Shapes: Tube laser cutting machines can cut a wide range of tube shapes—round, square, rectangular, and custom profiles—maximizing material use for multiple parts.
- Efficient Material Utilization: This versatility ensures that each tube is used as efficiently as possible, leaving minimal scrap.
- Reduced Need for Secondary Processing
- High-Quality Cuts: Clean, burr-free cuts reduce the need for additional processing, saving material and time.
- Precision Fit: Accurate cuts often eliminate the need for adjustments, further reducing waste.
- Automated Material Handling
- Efficiency and Accuracy: Automated loading and unloading reduce material handling errors, ensuring accurate cuts and minimizing material damage.
- Consistent Quality: Automation guarantees consistent cutting, reducing defects and part rejection rates.
- Environmental Benefits
- Less Scrap: By minimizing waste, tube laser cutting machines contribute to sustainable manufacturing practices, requiring fewer raw materials and reducing environmental impact.
How Does Tube Laser Cutting Machines Reduce The Risk of Tube Deformation?
- Precision Clamping and Support Systems
- Automated Clamping: These machines feature automated clamping systems that securely hold the tube in place during cutting, reducing the risk of movement or vibration that could cause deformation.
- Multiple Support Points: Tube laser cutting machines utilize multiple support points along the tube’s length, ensuring even weight distribution and preventing sagging or bending.
- Minimal Heat-Affected Zone (HAZ)
- Concentrated Laser Beam: The laser beam is highly concentrated, delivering precise cuts with minimal heat dispersion, which helps maintain a smaller heat-affected zone (HAZ) and reduces the risk of warping or deformation from heat.
- Non-Contact Cutting Process
- Laser Cutting Advantages: As a non-contact process, laser cutting eliminates physical interaction with the tube, preventing mechanical forces that could cause deformation, unlike traditional methods like sawing or drilling.
- Reduced Mechanical Stress: The lack of physical contact reduces the mechanical stress on the tube, preserving its shape throughout the cutting process.
- Precision Control and Automation
- Advanced Software Control: Sophisticated software controls the movement of the laser and the tube, ensuring consistent and precise cutting, and minimizing uneven cutting forces that could lead to deformation.
- Automated Adjustments: Some machines feature real-time monitoring systems that automatically adjust cutting parameters to maintain consistent conditions, further reducing deformation risks.
- Optimized Cutting Parameters
- Adjustable Laser Power and Speed: The ability to adjust laser power, speed, and focus based on material and tube thickness allows for fine-tuned settings that reduce excessive heat or force that could cause deformation.
- Pulse Cutting: For certain materials, pulse cutting is used to reduce continuous heat application, minimizing the risk of deformation.
- High-Quality Materials and Machine Design
- Rigid Machine Structure: The machine’s rigid structure minimizes vibrations during the cutting process, preventing distortion or deformation of the tube.
- Quality Components: High-quality, precision components such as linear guides and drives ensure smooth and accurate movement, reducing the likelihood of tube deformation.
- Customized Cutting Strategies
- Segmented Cutting: For long or thin tubes, segmented cutting can be employed to manage heat and stress distribution, reducing the risk of deformation.
- Cutting Sequence Optimization: The software can also optimize the cutting sequence to reduce heat buildup and stress in critical areas, further reducing deformation.
- Material-Specific Settings
- Material Database: Tube laser cutting machines often come with pre-programmed settings for various materials, ensuring that optimal cutting parameters are applied to each type of tube to avoid deformation.
How Long Is the Life of Tube Laser Cutting Machines?
- Laser Source Lifespan: The fiber laser source is a crucial component, typically lasting between 50,000 to 100,000 operating hours. This can translate to several years of use depending on the intensity of the operation. Machines used at higher intensities or for longer hours may experience a shorter laser lifespan.
- Machine Quality and Build: Machines from well-established manufacturers tend to have a longer lifespan due to their robust construction and high-quality components. Precision guides, durable materials, and well-designed mechanical parts contribute significantly to the machine’s overall longevity.
- Maintenance Practices: Consistent maintenance is essential to extend the life of the machine. Routine tasks include cleaning optics, checking alignment, lubricating moving parts, and replacing worn components. Neglecting these tasks can lead to premature wear, whereas proper maintenance helps prevent breakdowns and keeps the machine in peak working condition.
- Usage Intensity: Machines used in high-volume production environments may experience more wear and tear, potentially shortening their lifespan. In contrast, machines used intermittently for lower-volume production will likely last longer due to reduced strain on components.
- Environmental Conditions: The environment in which the machine operates plays a critical role in its longevity. Keeping the machine in a clean, controlled environment minimizes exposure to dust, moisture, and temperature fluctuations, all of which can negatively impact the machine’s performance and lifespan.
- Component Wear and Replacement: Key parts, such as the laser head, optics, and moving components, naturally wear out over time. Regular inspection and timely replacement of these components can help maintain performance and extend the machine’s overall service life.
- Software and Firmware Updates: Ensuring that the machine’s software and firmware are updated can help optimize performance and prevent software-related issues that could affect the machine’s longevity. Well-maintained software can also improve the overall functionality and efficiency of the cutting process.
Related Resources
Laser Marking VS Screen Printing
Laser Welding VS MIG Welding
Laser Rust Removal VS Sandblasting Rust Removal
Fiber Laser Cutting VS Plasma Cutting
Contact Us
Contact Information Form: