Introduction
Tube and Sheet Laser Cutting Machines
-
VIF-T Laser Cutting Machine
Rated 4.75 out of 5$34,300.00 – $179,000.00 Select options This product has multiple variants. The options may be chosen on the product page -
VIE-T Laser Cutting Machine
Rated 4.75 out of 5$43,300.00 – $188,000.00 Select options This product has multiple variants. The options may be chosen on the product page -
VIP-T Laser Cutting Machine
Rated 5.00 out of 5$68,800.00 – $213,500.00 Select options This product has multiple variants. The options may be chosen on the product page
Applications
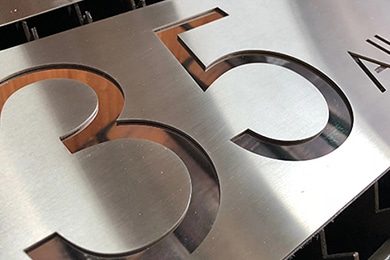
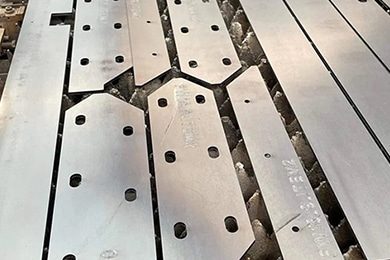
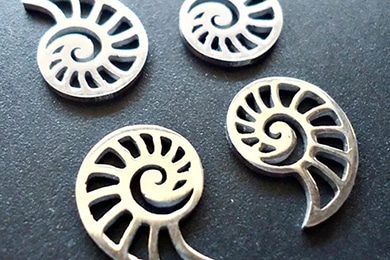
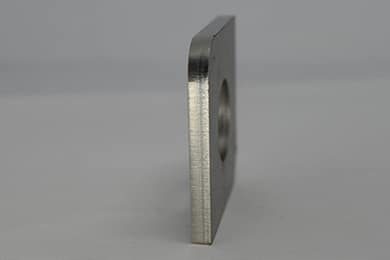
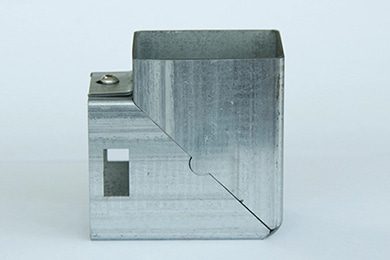
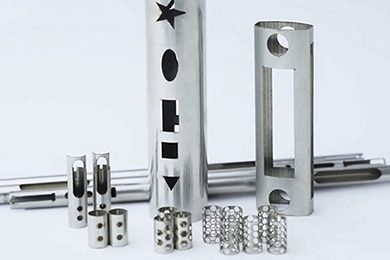
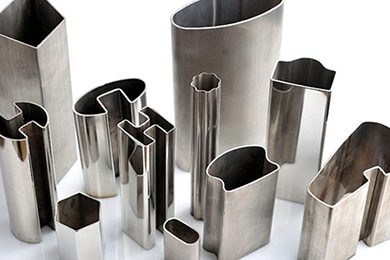
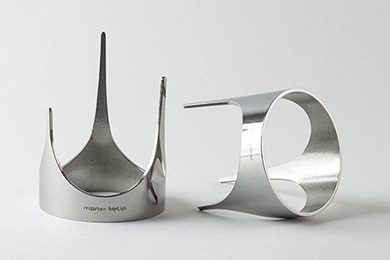
Advantages of Laser Cutting
High Precision and Accuracy
Laser cutting ensures exceptional precision, delivering clean, sharp cuts with tight tolerances, making it ideal for complex shapes and intricate designs without the need for additional finishing.
Versatility Across Materials
Tube and sheet laser cutting machines can cut a wide variety of materials, including stainless steel, aluminum, carbon steel, and more, making them suitable for diverse industries and applications.
Reduced Material Waste
The precision of laser cutting minimizes scrap material, optimizing material utilization and reducing overall production costs, leading to more sustainable and efficient manufacturing processes.
Speed and Efficiency
Laser cutting machines operate at high speeds, enabling faster production times and increased throughput, which is particularly beneficial for high-volume manufacturing and quick-turnaround projects.
Minimal Tool Wear and Maintenance
Unlike traditional cutting methods, laser cutting does not involve physical contact with the material, resulting in minimal tool wear, reduced maintenance requirements, and longer machine lifespans.
Flexibility in Design and Production
Laser cutting machines offer the ability to cut both flat sheets and tubes in a single setup, providing unmatched flexibility for manufacturers working with a range of shapes, sizes, and custom designs.
Advantages of Laser Cutting
Feature | Laser Cutting | Plasma Cutting | Waterjet Cutting | Flame Cutting |
Precision | Extremely high precision, fine cuts with minimal kerf width | Moderate precision, suitable for thicker materials | High precision, ideal for complex cuts | Lower precision, larger kerf width |
Material Versatility | Works with a wide range of metals, including thin and thick sheets | Best for thicker metals, especially mild steel | Suitable for metals, stone, ceramics, and composites | Works best with thicker steel and ferrous metals |
Speed | Fast, especially for thinner materials | Faster than laser for thicker metals | Slower than laser and plasma, especially on metals | Slower, typically used for thicker materials |
Edge Quality | Smooth, clean edges with minimal post-processing | Rougher edges, requiring more post-processing | Smooth edges with no heat-affected zone (HAZ) | Rougher edges, often requiring clean-up |
Heat Affected Zone (HAZ) | Minimal, reduces material distortion | Larger HAZ, can affect material properties | No heat-affected zone, ideal for sensitive materials | Larger HAZ, can distort thinner metals |
Material Thickness | Ideal for both thin and medium-thick materials | Best suited for medium to thick materials | Can cut both thin and thick materials, with high-quality edges | Primarily for thick materials (8mm+ in most cases) |
Cost Efficiency | Higher initial cost, but low operational cost and minimal waste | Lower initial cost, but higher operational cost due to consumables | High operating cost due to water usage and abrasives | Lower initial cost, but higher operational costs for fuel |
Maintenance | Low maintenance with minimal wear | Requires regular maintenance and consumable replacements | High maintenance due to pumps, abrasives, and nozzles | Requires regular maintenance, especially for cutting torches |
Customer Reviews
Frequently Asked Questions
What Are Tube and Sheet Laser Cutting Machines?
How Much Do Tube and Sheet Laser Cutting Machines Cost?
How Accurate Are Tube and Sheet Laser Cutting Machines?
- Cutting Tolerances: Most tube and sheet laser cutting machines achieve cutting tolerances within ±0.1 mm (±0.004 inches). High-end models can reach even tighter tolerances of ±0.05 mm (±0.002 inches) or better, depending on material and machine specifications.
- Repeatability: These machines are designed for excellent repeatability, ensuring that multiple parts produced from the same setup maintain consistent dimensions and shapes, minimizing the need for rework or adjustments.
- Beam Precision: Fiber lasers offer superior beam quality with a tight focus, which enhances cut precision. The narrow laser beam results in minimal kerf width (the width of the cut), producing cleaner, more accurate edges.
- Material and Thickness: The accuracy of the cuts can be influenced by the type and thickness of the material. While thinner materials provide better precision, thicker materials may have slightly larger tolerances due to the cutting process and the heat-affected zone.
- Control Systems: Modern laser cutting machines are equipped with advanced control systems that automatically adjust cutting parameters for different materials and thicknesses, further enhancing the machine’s accuracy.
- Maintenance: Regular maintenance and calibration are essential for preserving the machine’s accuracy over time. Proper upkeep ensures that the system continues to operate within its specified tolerances, minimizing the impact of wear and tear.
How Long Is the Life of Tube and Sheet Laser Cutting Machines?
- Machine Quality and Build
- High-Quality Machines: Premium machines from well-established manufacturers are designed to last 10 to 15 years or more. These machines are constructed with durable components and advanced technology, ensuring long-term reliability.
- Entry-Level Machines: More affordable models may have a shorter lifespan, generally ranging from 5 to 10 years due to the use of lower-grade materials and components.
- Usage and Workload
- Heavy Usage: Machines used in high-volume production or harsh environments tend to experience faster wear and tear, which can shorten their lifespan.
- Moderate Usage: Machines that undergo moderate workloads in optimal conditions can retain their performance for a much longer period.
- Maintenance and Care
- Regular Maintenance: Proper maintenance—routine checks, cleaning, and calibration—can significantly extend the machine’s life. Regular care ensures efficient operation and helps prevent breakdowns.
- Neglect: Failing to maintain the machine can lead to faster deterioration, reducing its overall lifespan.
- Technology Upgrades
- Technological Advancements: While the machine itself may last many years, technological developments may encourage businesses to upgrade to newer models with enhanced features. This does not necessarily make the older machine obsolete but reflects shifts in industry standards and efficiency.
- Components and Replacements
- Laser Source: The laser source typically lasts between 10,000 to 20,000 hours of operation, depending on the type and intensity of use. Replacing the laser source may be necessary midway through the machine’s life.
- Additional Components: Components like optics, motors, and control systems might require replacement or maintenance over time, affecting the machine’s overall lifespan.
What Materials Can Tube and Sheet Laser Cutting Machines Cut?
- Stainless Steel: Known for its versatility and strength, stainless steel is one of the most commonly cut materials with fiber lasers. It offers high precision and is widely used in the automotive, aerospace, and medical industries.
- Carbon Steel: Fiber lasers excel at cutting carbon steel, whether in thin sheets or thick plates. It is a popular choice for structural components and general fabrication due to its strength and availability.
- Aluminum: While aluminum presents challenges due to its reflective surface, fiber lasers can cut this material effectively with the right settings. It is commonly used in industries like aerospace, automotive, and construction.
- Brass: Brass, valued for its decorative qualities and electrical conductivity, can be efficiently cut by fiber lasers, though special care is required due to its reflectivity.
- Copper: Copper’s high reflectivity and electrical conductivity make it challenging to cut, but modern fiber lasers can handle it with the appropriate settings. It’s often used in electrical and thermal applications.
- Titanium: With its strength and resistance to corrosion, titanium is ideal for aerospace, medical, and high-performance applications. Fiber lasers can cut titanium with excellent precision.
- Nickel Alloys: Used in high-temperature and corrosion-resistant applications, nickel alloys can be effectively cut by fiber lasers, although specific settings may be required.
What Are The Maintenance Requirements For Tube and Sheet Laser Cutting Machines?
- Daily Maintenance
- Clean the Machine: Remove dust and debris from the machine’s surface and cutting area. Clean the optical lenses to maintain laser performance and prevent damage.
- Check Laser Path: Ensure the laser beam path is clear and properly aligned. Misalignment can degrade cutting accuracy and quality.
- Inspect the Cooling System: Check the coolant levels and look for leaks or blockages. Proper cooling is essential to avoid overheating.
- Weekly Maintenance
- Lubricate Moving Parts: Apply lubricant to moving components such as rails and gears to minimize friction and wear.
- Check and Clean Filters: Inspect and clean air filters. Replace them if dirty to ensure proper ventilation. Clean the dust collection system regularly.
- Examine Electrical Connections: Ensure all electrical connections are secure, free of corrosion, and undamaged.
- Monthly Maintenance
- Calibrate the Machine: Perform calibration checks to ensure cutting accuracy. This includes adjusting the laser beam, focus, and other cutting parameters.
- Inspect Optics: Check the mirrors and lenses for wear and cleanliness. Use recommended cleaning solutions to prevent scratches and ensure clear focus.
- Check Gas Supply: Ensure that the assist gas supply (e.g., nitrogen or oxygen) is sufficient, and inspect the gas lines for leaks.
- Quarterly Maintenance
- Inspect Drive System: Examine belts, pulleys, and motors for signs of wear. Replace worn components to maintain smooth operation and prevent breakdowns.
- Software Updates: Check for any available software updates for the machine’s control system. Regular updates improve performance and address potential issues.
- Annual Maintenance
- Professional Servicing: Schedule a comprehensive inspection by a qualified technician. This includes checking the laser source, electrical systems, and mechanical components.
- Replace Consumables: Depending on usage, replace consumables such as nozzles, filters, and lenses that may have degraded over time.
How Much Do Tube And Sheet Laser Cutting Machines Cost To Operate?
- Energy Consumption
- Power Consumption: Laser-cutting machines can consume a significant amount of electricity, typically between 15 to 25 kWh, translating to an hourly cost of approximately $1.50 to $2.50, depending on local electricity rates.
- Cooling Systems: Additional energy is required for cooling systems to maintain optimal operating temperatures for the laser source and other machine components.
- Consumables
- Assist Gas: The cost of assist gases such as nitrogen, oxygen, or air varies by material and usage. For nitrogen and oxygen, costs can range from $10 to $30 per hour based on the consumption rate.
- Optics and Lenses: Over time, lenses and mirrors may need to be replaced due to wear. Replacement costs typically range from $500 to $1,000 annually, depending on usage.
- Nozzles and Consumables: Nozzles and other parts require periodic replacement, adding to overall consumable costs.
- Maintenance
- Routine Maintenance: Regular maintenance, including cleaning, calibration, and lubrication, can cost approximately $1,000 to $2,000 per year, depending on the machine’s usage.
- Professional Servicing: Annual or bi-annual professional servicing typically costs between $1,000 to $3,000, depending on service complexity and provider.
- Labor
- Operator Costs: Skilled operators are required to run and maintain the machines. Depending on region, operator wages typically range from $20 to $40 per hour.
- Training: Initial and ongoing training costs are important for ensuring operators are proficient and minimizing operational errors.
- Depreciation and Financing
- Depreciation: The machine’s initial cost is spread over its useful life. For example, a $100,000 machine with a 10-year lifespan incurs an annual depreciation cost of $10,000.
- Financing: If the machine is financed, interest costs will further impact the overall operating expenses.
- Material Costs
- Raw Materials: The cost of raw materials (metal sheets and tubes) varies depending on type and thickness, impacting the overall operational cost.
- Estimated Total Operating Cost
- Total Costs: Combining all factors, the estimated operating cost for a tube and sheet laser cutting machine can range from $50 to $100 per hour. Actual costs will vary based on machine specifications, usage, and local conditions.
What Safety Features Are Included With Tube And Sheet Laser Cutting Machines?
- Enclosed Design: Many laser cutting machines feature a fully enclosed design, which helps contain the laser beam within the cutting area. This minimizes the risk of accidental exposure to the high-powered laser. Enclosures are often equipped with safety interlocks that prevent the laser from operating if the enclosure is open.
- Safety Interlocks: These interlocks prevent the machine from running when any access doors or panels are open. This ensures that the laser beam remains contained and no one can accidentally come into contact with the laser or moving parts while the machine is in operation.
- Emergency Stop Buttons: Emergency stop buttons are strategically placed around the machine, including on the control panel, for quick access. These buttons allow operators to halt the machine’s operation immediately in case of an emergency, ensuring a rapid response to potentially dangerous situations.
- Laser Safety Glass: Machines with viewing windows typically use laser safety glass. This specialized glass blocks harmful laser radiation, allowing operators to safely observe the cutting process without risking eye injury.
- Fume Extraction Systems: Laser cutting produces harmful fumes and particulates, especially when cutting metals. Integrated fume extraction systems are used to capture and remove these emissions, improving air quality and reducing the risk of inhaling hazardous substances.
- Collision Detection: Some advanced machines feature collision detection sensors that monitor potential collisions between the cutting head, material, or machine bed. These sensors can automatically stop or adjust the machine’s operation to prevent damage to the equipment and ensure operator safety.
- Control System Alerts: Modern laser-cutting machines come with intelligent control systems that detect errors or malfunctions. These systems can issue visual or audible alerts to warn operators of issues, enabling quick intervention to prevent accidents.
- Access Control: Access control features are often included to restrict machine operation to authorized personnel only. This can involve password protection or keycard access, which helps prevent untrained or unauthorized individuals from using the machine.
- Software Safeguards: Many laser cutting machines are equipped with advanced control software that includes safeguards to ensure the machine operates within safe parameters. These safeguards can prevent the machine from running with incorrect settings or operator errors, reducing the risk of accidents.
Related Resources
Laser Marking VS Screen Printing
Laser Welding VS MIG Welding
Laser Rust Removal VS Sandblasting Rust Removal
Fiber Laser Cutting VS Plasma Cutting
Contact Us
Contact Information Form: