Quality Assurance
At Victory Industry, our commitment to quality is unwavering and embedded in every aspect of our operations. We adhere to strict quality assurance processes to ensure that our smart laser equipment not only meets but exceeds the highest industry standards. Our commitment to quality extends throughout the entire product lifecycle, from design and manufacturing to delivery and customer support.
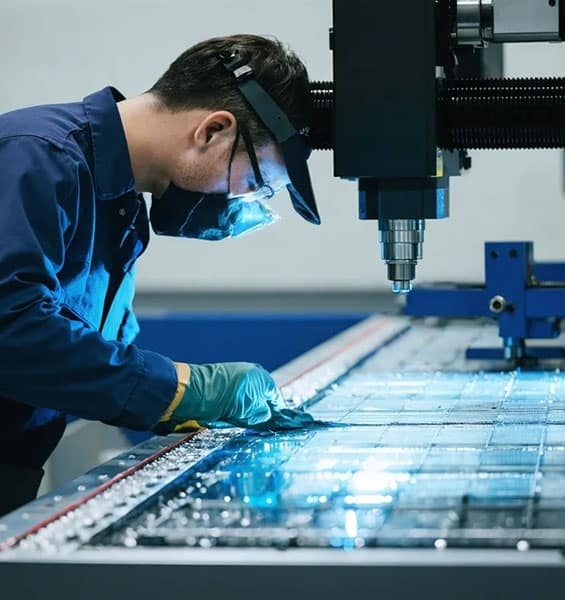
Strict Manufacturing Standards
Our manufacturing facilities operate to strict standards to guarantee the quality of every smart laser device that carries the Victory Industry name. We use advanced quality control processes at every stage of production to ensure that every component and system is thoroughly tested and inspected before being integrated into the final product.
Supplier Quality Management
Victory Industry takes the quality of the components purchased from our suppliers very seriously. Our supplier quality management program involves rigorous evaluation and auditing to ensure that the materials and parts we receive meet our strict standards. This meticulous approach extends our commitment to quality beyond our own facilities and into our supply chain.
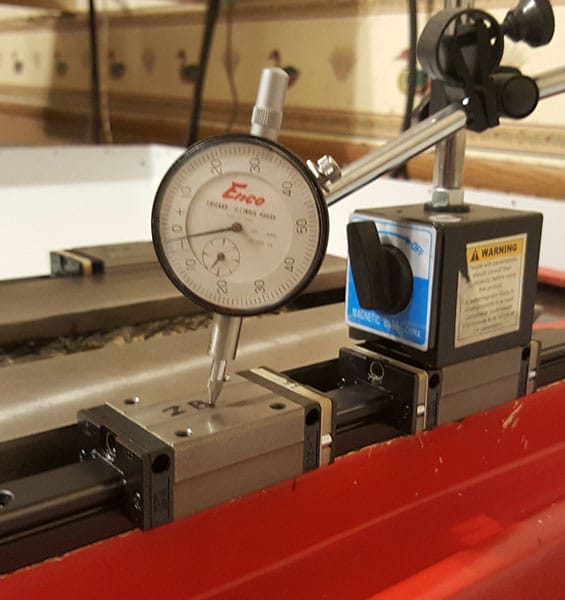
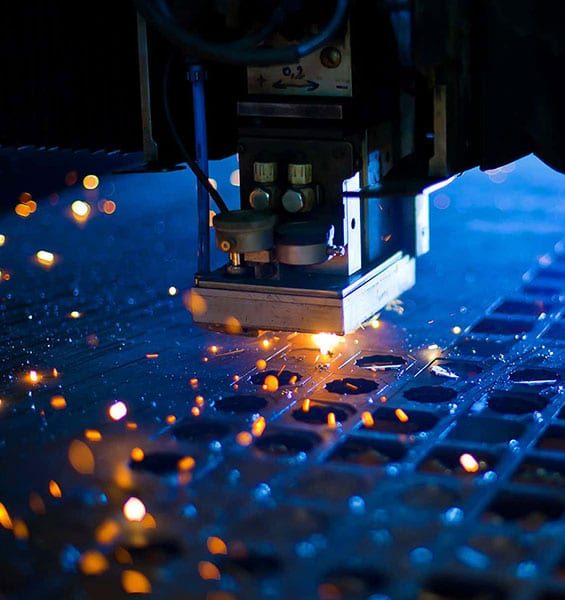
Comprehensive Testing Protocol
Victory Industry’s quality assurance involves a comprehensive testing regime. Every laser solution is rigorously tested for precision, accuracy, and reliability. Our advanced testing protocols include functional testing, stress testing, and performance evaluation to ensure our equipment consistently delivers optimal results in real-world manufacturing environments.
Customer-Focused Quality Assurance
Customer satisfaction is our top priority in quality assurance. We actively seek feedback from our customers and use it to guide our quality improvement programs. Our customer-centric approach means we are able to respond to our customer’s changing needs, driving us to continuously improve the quality of our laser solutions.
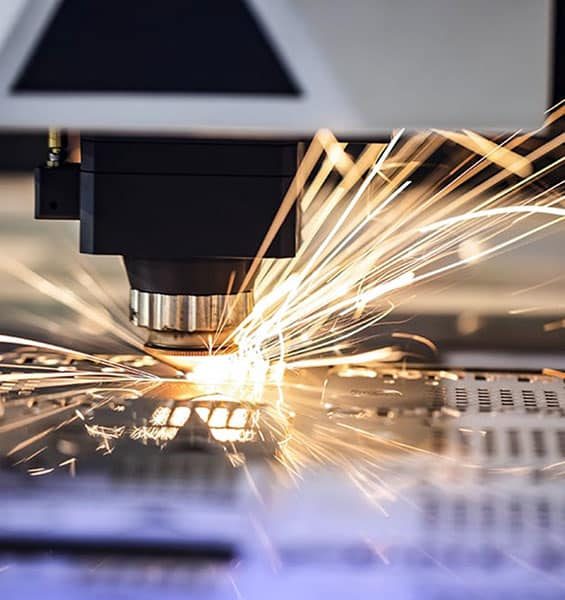